ボールミル粉砕法には数多くの利点があり、様々な産業で広く利用されています。その主な利点は、費用対効果が高いこと、操作が簡単なこと、粒径が10ミクロン程度の微粉末を製造できることなどである。さらに、湿式・乾式どちらの粉砕プロセスにも適しており、密閉容器システムにより無菌性を維持し、有毒物質や研磨性物質の粉砕にも効果的である。また、この方法は連続運転に対応し、エネルギー消費量が少なく、メンテナンスとスペースが最小限で済む。さらに、プロセス中に結晶欠陥を生成することは、特定の用途に有利である。
キーポイントの説明
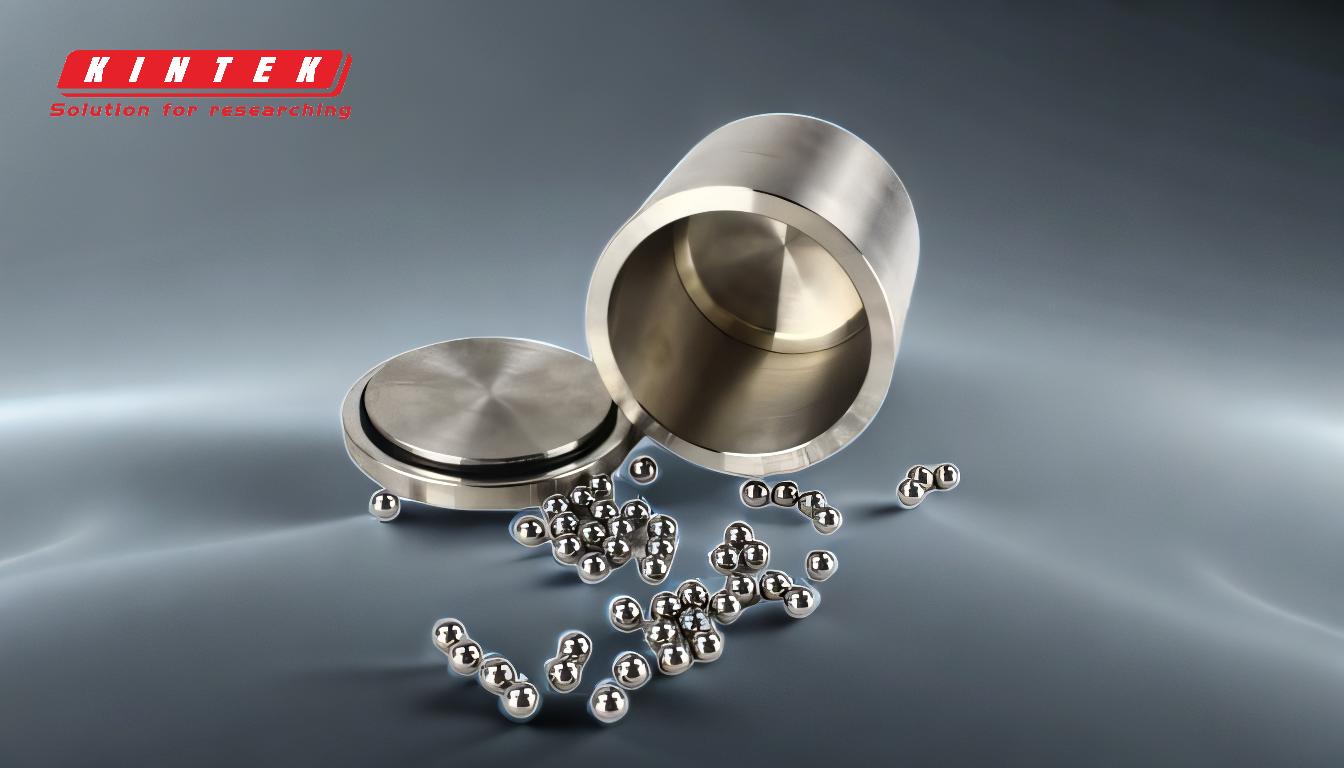
-
費用対効果と操作性
- ボールミル粉砕は、他の粉砕技術に比べて安価な方法であるため、様々な用途に利用することができます。
- プロセスは単純で簡単で、技術的な専門知識は最低限で済みます。
- この低コストと簡便さの組み合わせにより、小規模から工業的用途まで、好んで選ばれている。
-
微粉末の生産
- ボールミルは、粒径10ミクロン以下の非常に微細な粉末を製造することができます。
- 医薬品、セラミックス、ナノ材料など、高い表面積や均一な粒子分布が要求される用途では、このような微細な粒子径が重要です。
-
湿式・乾式粉砕への適合性
- ボールミルは汎用性が高く、湿式粉砕と乾式粉砕の両方に使用できます。
- 湿式粉砕はスラリー状が必要な材料に有効で、乾式粉砕は水分を加えない微粉末の製造に最適です。
-
無菌性の維持
- ボールミルの密閉容器システムは、製薬産業や食品産業での用途に不可欠な無菌性を保証します。
- コンタミネーションを防ぎ、デリケートな材料の完全性を維持します。
-
低エネルギー消費
- ボールミル粉砕はエネルギー効率が高く、運転コストと環境への影響を低減します。
- このプロセスは、粉砕メディア(ボール)の運動エネルギーを利用して粒子径の減少を達成することにより、エネルギー使用を最適化します。
-
有害物質や研磨材の取り扱い
- ボールミルは、密閉設計により有害物質への暴露を防ぐため、有毒物質の粉砕に適しています。
- また、磨耗しやすい材料の粉砕にも効果的です。
-
連続運転が可能
- ボールミルは連続運転が可能で、大規模な生産工程に最適です。
- この特徴により、安定した生産量が確保され、ダウンタイムが短縮されるため、生産性が向上します。
-
低メンテナンスと省スペース
- ボールミルはメンテナンスが最小限で済むため、長期的な運転コストを削減できます。
- コンパクトな設計で限られたスペースに設置できるため、スペースに制約のある施設に適しています。
-
結晶欠陥の生成
- ボールミリングプロセスでは、材料に結晶欠陥を導入することができる。
- これらの欠陥は、材料の触媒活性、機械的強度、導電性などの特性を向上させることができる。
-
幅広いアプリケーション
- ボールミリングは、製薬、セラミックス、冶金、ナノテクノロジーなど、さまざまな産業で使用されています。
- その汎用性と適応性により、材料加工と合成のための貴重なツールとなっている。
要約すると、ボールミル法は、その費用対効果、汎用性、特定の特性を持つ微粉末を製造する能力により、非常に有利な技術である。有毒物質や摩耗性物質の取り扱いにも適しており、エネルギー消費量も少なく、メンテナンスも最小限で済むため、工業用や研究用としてさらに魅力的な手法である。
総括表
利点 | 概要 |
---|---|
コストパフォーマンス | 他の粉砕技術に比べ安価で、小規模から大規模まで理想的。 |
微粉末製造 | 高表面積のニーズに不可欠な10ミクロンの微粒子を生産。 |
湿式・乾式粉砕 | 湿式・乾式両方に対応し、多様な材料に適しています。 |
無菌性維持 | クローズドコンテナシステムにより、コンタミネーションのない処理を実現 |
低エネルギー消費 | エネルギー効率に優れ、運転コストと環境への影響を低減します。 |
有害物質や摩耗性物質にも対応 | 密閉設計により、有害物質への暴露を防ぎ、摩耗に耐えます。 |
連続運転 | 安定した生産量と最小限のダウンタイムで、大規模生産に最適です。 |
低メンテナンスと省スペース | スペースに制約のある施設でも、最小限のメンテナンスとコンパクトな設計を実現。 |
結晶欠陥の生成 | 触媒活性や機械的強度などの材料特性を高める |
幅広い用途 | 製薬、セラミックス、冶金、ナノテクノロジーで使用されています。 |
ボールミルによる材料加工の強化はいかがですか? 今すぐ までご連絡ください!