プラズマ・スパッタリングは、真空環境でターゲット材料に高エネルギーのイオン(通常はアルゴン)を照射することにより、基板上に薄膜を形成する高度な物理蒸着(PVD)技術である。このプロセスでは、不活性ガス原子がイオン化され、負に帯電したターゲット材料に向かって加速される。イオンとターゲットの衝突により、ターゲットから原子が放出され、基材上に堆積し、薄く均一なコーティングが形成される。プラズマスパッタリングは、精密で高品質な膜を作ることができるため、半導体製造、光学コーティング、工具コーティングなど、さまざまな産業で広く使用されている。
ポイントを解説
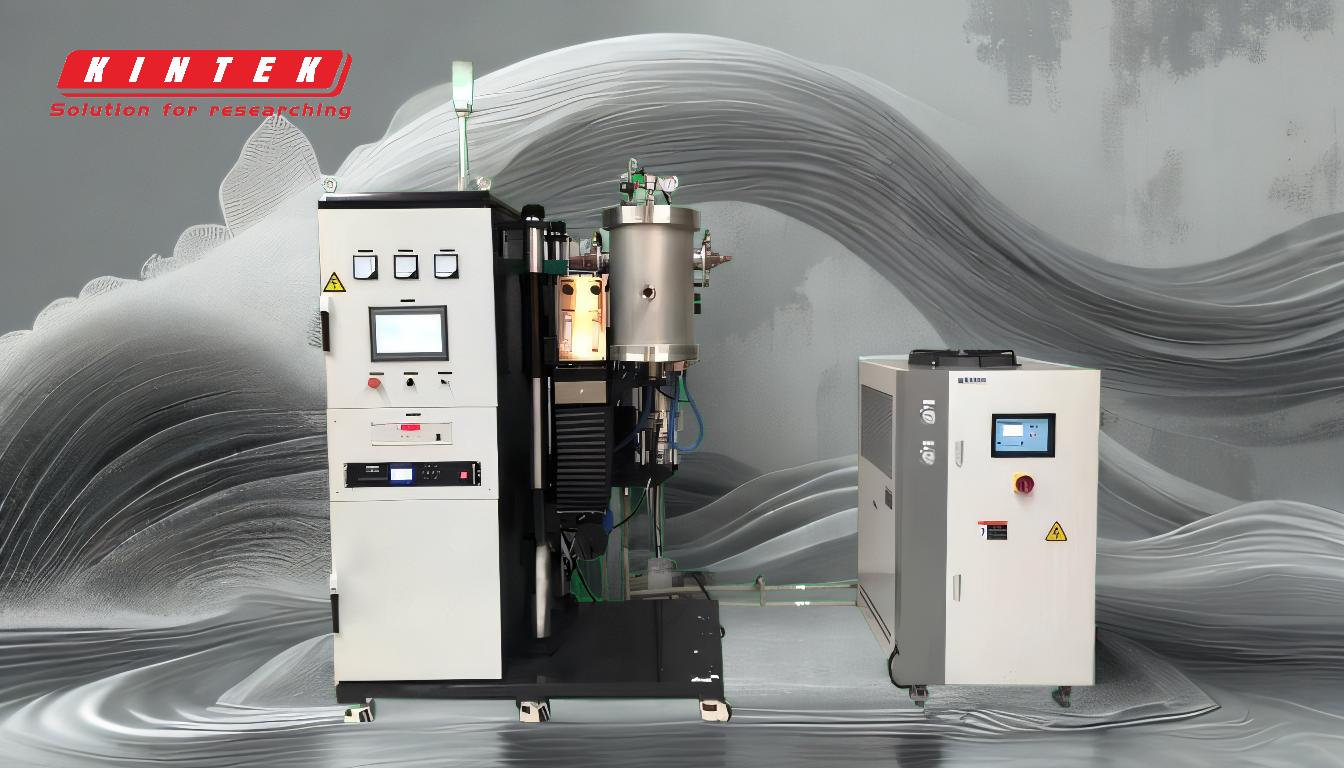
-
プラズマスパッタリングの基本メカニズム:
- プラズマスパッタリングでは、真空チャンバーを使用してアルゴンガスをイオン化し、プラズマを形成する。
- コーティングの元となるターゲット材料は、負に帯電した陰極に接続される。
- コーティングが成膜される基材は、プラスに帯電した陽極に接続される。
- プラズマ中の自由電子がアルゴン原子と衝突してイオン化し、正電荷を帯びたアルゴンイオンが生成される。
- これらのイオンは電界によってターゲット物質に向かって加速され、ターゲットから原子が放出される。
-
エネルギー移動とターゲット原子の放出:
- 高エネルギーのアルゴンイオンがターゲット材料に衝突すると、その運動エネルギーがターゲット原子に伝達される。
- このエネルギー伝達により、ターゲット原子はスパッタリングと呼ばれるプロセスで表面から放出される。
- 放出された原子は真空チャンバー内を移動し、最終的に基板上に凝縮して薄膜を形成する。
-
薄膜の蒸着:
- 放出されたターゲット原子は真空チャンバー内を拡散し、基板上に堆積する。
- この蒸着プロセスにより、基板に原子レベルで強く密着する薄く均一なコーティングが得られる。
- この方法は、正確な膜厚と組成の膜を作ることができるため、高い精度が要求される用途に最適です。
-
プラズマスパッタリングの用途:
- 半導体製造:集積回路やその他のマイクロエレクトロニクス部品の製造に使用される。
- 光学コーティング:ガラスに反射防止膜や高放射率膜を形成する。
- ツールコーティング:切削工具の耐久性と性能を向上させます。
- データ保存:CD/DVDコーティングの製造に使用されます。
-
プラズマスパッタリングの利点:
- 精度と均一性:このプロセスは、高性能アプリケーションに不可欠な、非常に薄く均一な膜の成膜を可能にします。
- 汎用性:金属、合金、セラミックスなど幅広いターゲット材に使用可能。
- 強力な接着力:ターゲット原子の高エネルギー衝突により、基材との強固な結合が保証され、耐久性の高いコーティングが実現する。
-
課題と考察:
- 熱管理:このプロセスではかなりの熱が発生するため、最適な状態を維持するための特殊な冷却システムが必要となる。
- 真空要件:高真空環境が必要なため、装置の複雑さとコストが増加する可能性がある。
- ターゲットの侵食:ターゲット材への連続的なスパッタリングは、ターゲット材の浸食を招き、定期的な交換が必要となる。
プラズマ・スパッタリングは、卓越した精度と品質で薄膜を成膜するための非常に効果的で汎用性の高い技術である。その応用範囲は様々な産業に及び、現代の製造および技術開発において重要なプロセスとなっている。
総括表
アスペクト | 詳細 |
---|---|
メカニズム | 真空チャンバー内でアルゴンガスをイオン化し、ターゲット物質原子を射出する。 |
用途 | 半導体製造、光学コーティング、工具コーティング、データストレージ |
利点 | 精密さ、均一性、汎用性、強力な接着性。 |
課題 | 熱管理、真空要件、ターゲットの侵食。 |
プラズマスパッタリングにご興味がおありですか? 当社の専門家に今すぐご連絡ください までご連絡ください!