熱分解リアクターの設計には、プロセス要件、原料特性、運転目標を包括的に理解することが必要である。設計は、効率性、安全性、および特定の原料や所望の出力への適応性を確保しなければならない。主な検討事項には、反応器のタイプ(バッチ式か連続式か)、サイズ、加熱機構、ガス処理や製品分離などの補助システムとの統合などがある。以下では、熱分解リアクターの設計に不可欠な側面を説明する。
キーポイントの説明
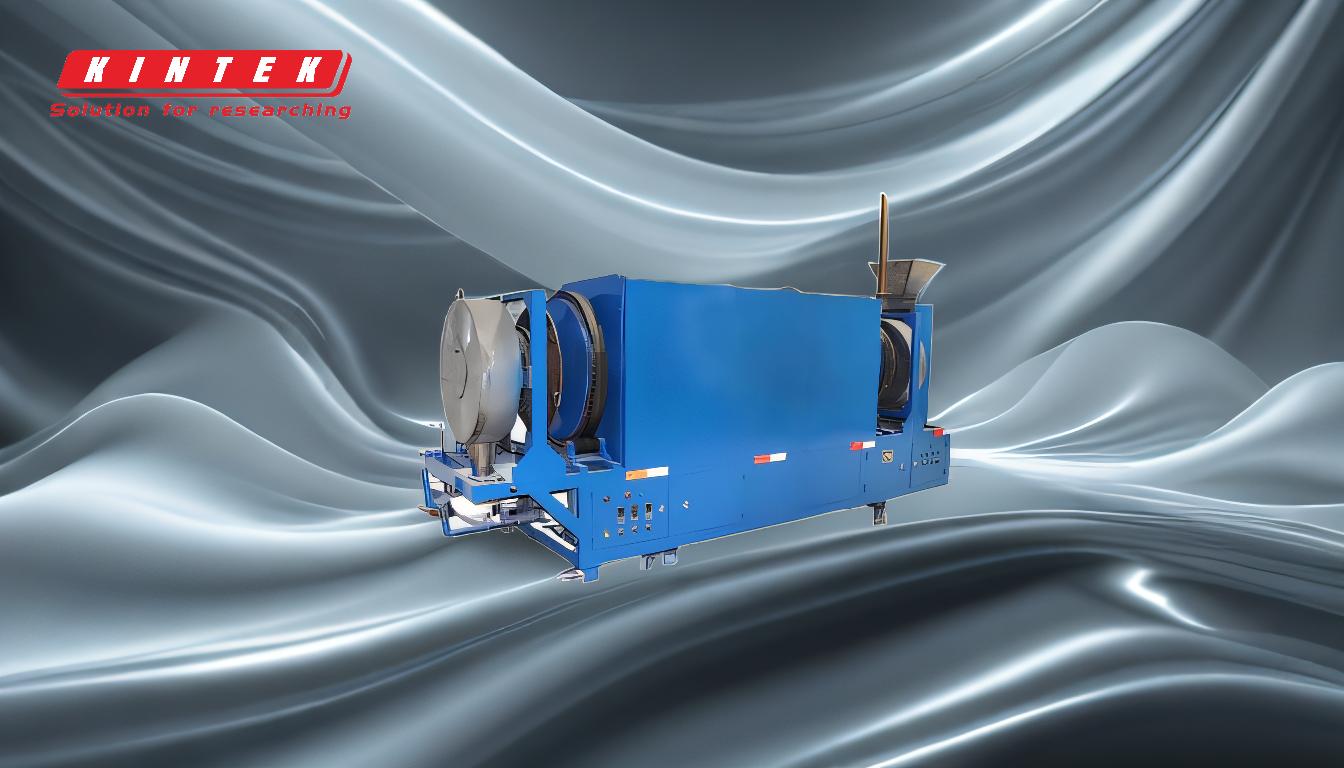
-
運転上の必要性に基づいて原子炉のタイプを決定する:
- バッチ式反応器と連続式反応器:バッチリアクターは、小規模の操業や限られた原料を処理する場合に適している。コスト効率が高く、操作も簡単であるが、効率が低い場合がある。一方、連続式リアクターは、高い処理能力と自動化を必要とする大規模な操作に理想的である。エネルギー効率に優れ、安定した生産量が得られるが、初期コストが高くなる。
- 決定要因:原料の入手可能性、予算、希望する自動化レベルに基づいて選択する。例えば、原料を継続的に供給でき、予算が高い場合は 連続熱分解リアクター が望ましい。
-
適切なサイズと容量を選ぶ:
- 原料量:リアクターのサイズは、処理しようとする原料の量に合わせるべきである。小規模処理にはコンパクトなリアクターで十分であるが、工業規模の処理にはより大きなリアクターが必要である。
- スケーラビリティ:必要に応じて将来的な拡張が可能な設計であること。モジュラー設計は、オペレーションの拡張に有利である。
-
加熱メカニズムを考える:
- 直接暖房と間接暖房:直接加熱では原料を熱源にさらすが、間接加熱では熱交換器を使用する。間接加熱の方が、温度管理がしやすく、コンタミネーションのリスクが少ないため、好まれることが多い。
- 熱源:一般的な熱源には、電気ヒーター、ガスバーナー、他の工程からの廃熱などがある。その選択は、コスト、利用可能性、エネルギー効率に依存する。
-
補助システムの統合:
- ガスハンドリング:熱分解により合成ガスが発生するが、これを安全に捕集して処理しなければならない。ガス収集、冷却、精製のためのシステムを設計する。
- 製品分離:バイオ炭、バイオオイル、合成ガスを効果的に分離するために、反応器にはサイクロン、凝縮器、急冷器を統合する必要がある。
- 安全システム:安全運転を確保するため、圧力逃し弁、温度センサー、緊急シャットダウン機構を含む。
-
原料特性の最適化:
- 素材タイプ:原料(プラスチック、ゴム、バイオマスなど)が異なれば、熱的性質や分解温度も異なる。これらのばらつきに対応できるように反応器を設計する。
- 前処理要件:原料によっては、熱分解の前に乾燥や破砕が必要な場合がある。反応器の設計が前処理された原料を効率的に処理できることを確認する。
-
エネルギー効率と環境コンプライアンスの確保:
- 熱回収:廃熱を再利用する熱回収システムを取り入れ、全体的なエネルギー効率を向上させる。
- 排出規制:排出を最小限に抑え、環境規制に適合するようにリアクターを設計する。これには、ガス処理のためのスクラバーやフィルターが含まれる場合がある。
-
コストとメンテナンスの評価:
- 初期投資:初期コストと長期的な運転上の利点のバランスをとる。例えば、連続式リアクターは、イニシャルコストは高いが、長期的な運転コストは低いかもしれない。
- メンテナンス要件:ダウンタイムとメンテナンスコストを最小限に抑える設計を選択しましょう。耐久性のある材料やアクセスしやすい部品は、メンテナンスの手間を軽減することができる。
これらの要素を注意深く考慮することで、特定の運転ニーズを満たし、効率を最大化し、安全性と環境コンプライアンスを確保する熱分解リアクターを設計することができます。バッチ式、連続式のいずれを選択するにしても、重要なのは、供給原料、予算、生産目標に合わせた設計を行うことである。
総括表
キーアスペクト | 詳細 |
---|---|
リアクタータイプ | バッチ式(小規模、費用対効果)または連続式(大規模、自動化) |
サイズと容量 | 原料の量に合わせ、将来の拡張性を確保する。 |
加熱メカニズム | 直接(露光)または間接(熱交換器);熱源を賢く選択する |
補助システム | ガスハンドリング、製品分離、安全機構 |
原料の最適化 | 原料の種類と前処理要件に対応 |
エネルギー効率 | 熱回収と排出抑制システムを組み込む |
コストとメンテナンス | 初期投資と長期的な操業メリットのバランス |
お客様のニーズに合わせた熱分解リアクターの設計はいかがですか? 当社の専門家に今すぐご連絡ください にお問い合わせください!