蛍光X線(XRF)分析用のプレスされたペレットを準備することは、正確で信頼性の高い結果を得るための重要なステップです。このプロセスでは、サンプルを微粉末に粉砕し、バインダーと混合し、高圧下で圧縮して均質なペレットを形成します。この方法はサンプルの均質性を高め、空隙をなくし、サンプルの希釈を減らし、より良い分析結果につながります。プレスペレットは、その利便性、費用対効果、信頼性から広く使用されており、蛍光X線分析試料前処理の業界標準となっています。
主なポイントの説明
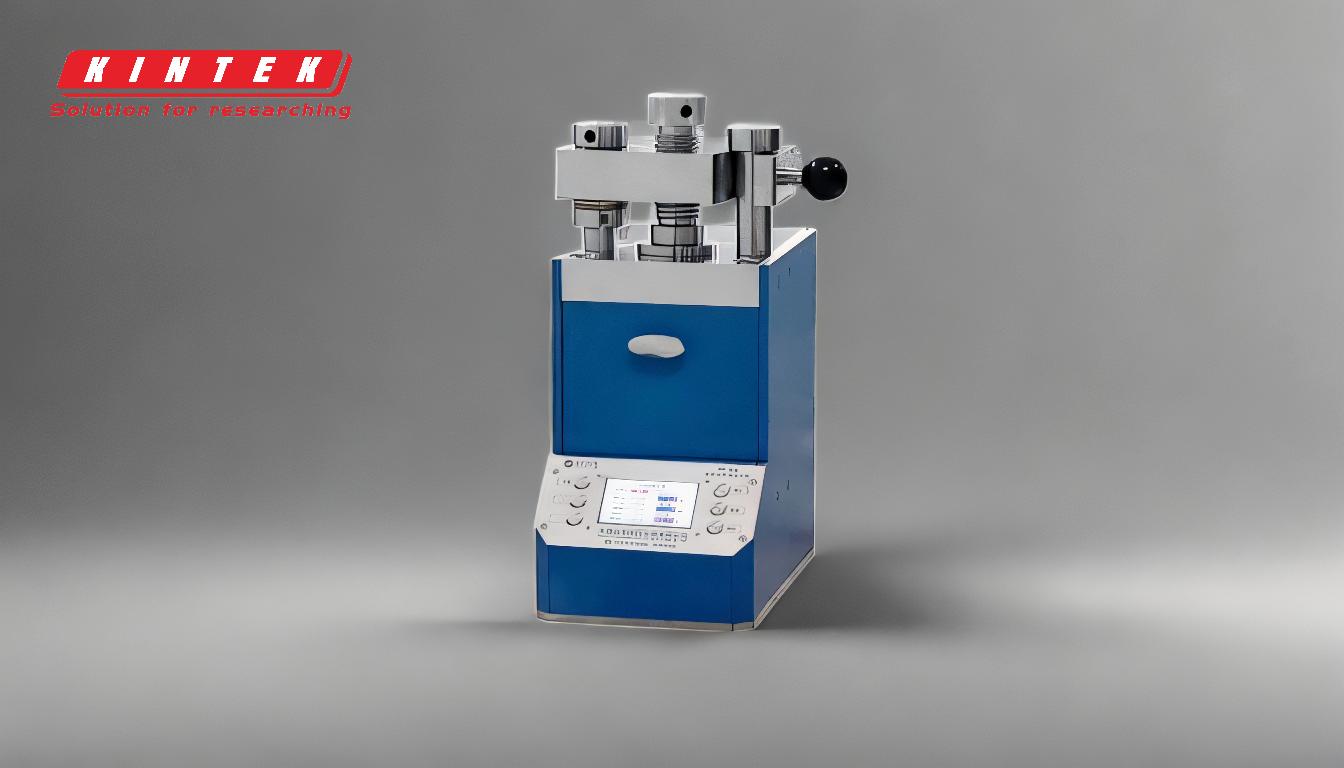
-
サンプルを微粉砕する:
- プレスされたペレットを調製する最初のステップは、サンプルを粉砕して粒度を細かくすることである。理想的な粒子径は75µm以下で、50µm以下が最適です。粒子径を小さくすることは、均質性を高め、蛍光X線分析の精度に影響を及ぼす粒子径効果のリスクを低減するために極めて重要である。粉砕は、粉砕機または同様の装置を用いて行うことができる。
-
バインダーとの混合:
- 粉砕後、粉末試料はバインダーまたは粉砕助剤と混合される。一般的なバインダーにはセルロースワックス混合物があり、圧縮時に粒子を結合させるのに役立つ。一般的なバインダーとサンプルの比率は20~30%です。バインダーは試料がよく付着し、亀裂や空隙のない強固なペレットを形成することを保証します。
-
混合物をプレスしてペレットにする:
- 粉末試料とバインダーの混合物は、次にプレス金型に流し込まれる。このダイは試料を高圧下で保持するように設計されており、一般的には15トンから40トンの間であるが、最も一般的な範囲は20トンから30トンである。高圧は混合物を圧縮し、緻密で均質なペレットを形成する。この工程は、空隙をなくし、正確な蛍光X線分析に不可欠な試料の均一分散を確実にするため、非常に重要です。
-
プレスペレットの利点
- プレスペレットは、ルースパウダーや他の試料調製方法と比較していくつかの利点がある。均質で空隙がないため、ほとんどの元素で高い強度が得られ、より良い分析結果が得られます。プレスペレットは、ppm範囲の微量元素の分析に特に有用である。さらに、調製は比較的簡単で安価であり、粉砕機やサンプルプレスのような基本的な装置を必要とするだけである。
-
考慮点と限界:
- プレスペレットは非常に効果的であるが、限界がないわけではない。特に主要元素については、粒子径の影響や鉱物学的な影響を受けやすい。したがって、これらの影響を最小限に抑えるためには、試料を適切な粒子径に粉砕し、バインダーを試料と十分に混合することが不可欠です。
-
自動プレスと手動プレス:
- プレスされたペレットは、自動化されたシステムまたは手動のプレス機を用いて製造することができる。自動化システムはより迅速で安定性が高く、ハイスループットのラボに適している。一方、手動のプレス機はコスト効率が高く、小規模のラボや分析頻度の低いラボで使用できる。どちらの方法でも、粉砕、混合、プレスの手順が正しく行われていれば、高品質のペレットを作ることができます。
これらのステップに従うことで、蛍光X線分析用の高品質プレスペレットを調製し、正確で信頼性の高い結果を得ることができます。このプロセスは簡単でコスト効率が高く、業界で広く使用されているため、蛍光X線分析を行うラボには必須の技術です。
要約表
ステップ | キー詳細 |
---|---|
粉砕 | 粒度<75µm(最適<50µm)を達成し、均質性を高める。 |
バインダーとの混合 | 接着性を確保し、ひび割れを防ぐため、バインダー(セルロースワックスなど)を20~30%使用する。 |
プレス | 20~30トンの圧力をかけ、緻密で均質なペレットを形成する。 |
利点 | 均質性を高め、希釈を減らし、分析精度を向上させる。 |
制限事項 | 主要元素の粒子径と鉱物学的影響を受けやすい。 |
自動化と手動の比較 | ハイスループット・ラボには自動化システム、費用対効果には手動プレス。 |
蛍光X線分析用のプレスペレットの準備にお困りですか? 当社の専門家に今すぐご連絡ください オーダーメイドのソリューションを