ボールミルの生産量を増やすには、粉砕性能に影響する様々な要因を最適化する必要がある。主な要因には、回転速度、粉砕媒体のサイズと種類、材料の特性、ミルの充填率、供給速度や滞留時間などの運転パラメータなどがあります。これらの変数を注意深く調整することで、ボールミルの効率と生産量を向上させることができる。これには、適切なボールサイズと密度の選択、最適なL:D比の維持、粉砕された製品のタイムリーな除去、供給速度と粉砕能力のバランスなどが含まれます。以下では、ボールミルで生産量を増やす方法について包括的に理解するために、これらの要因について詳しく説明します。
キーポイントの説明
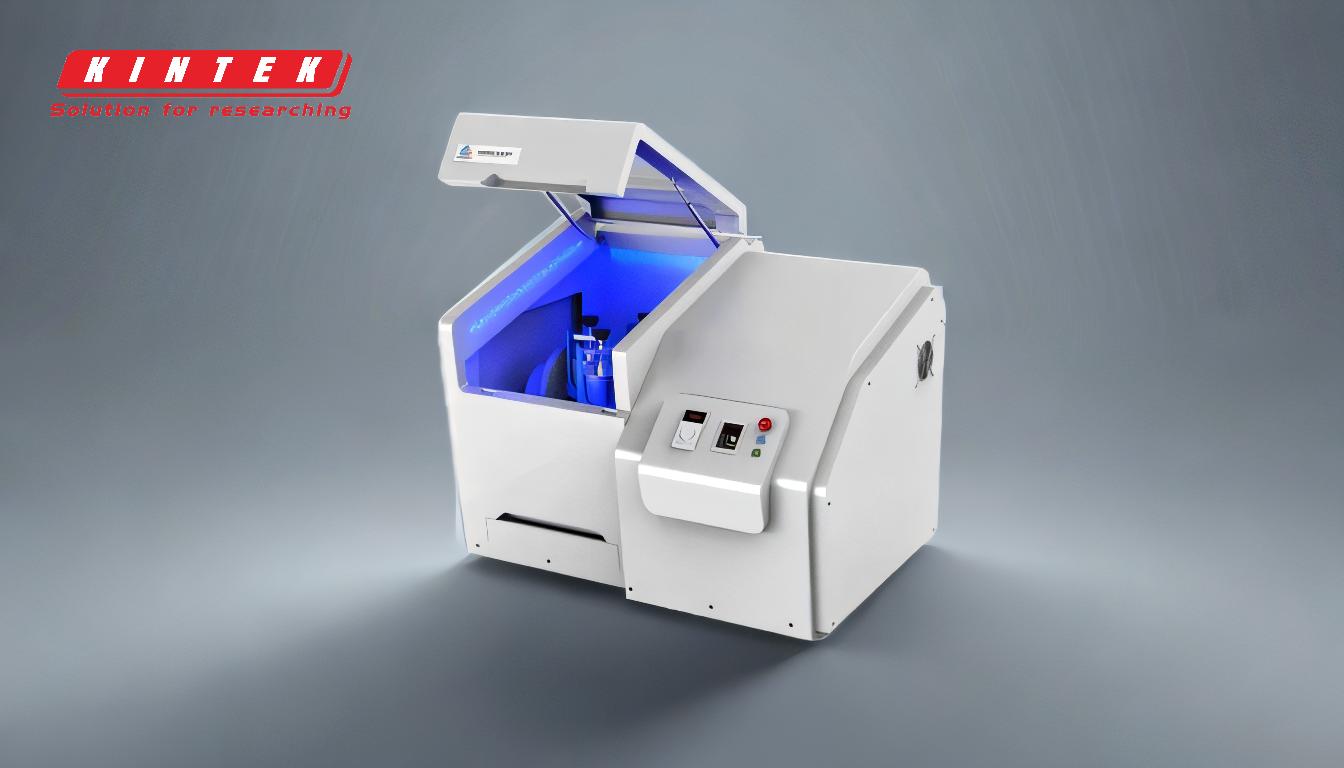
-
回転速度の最適化
- ボールミルの回転速度は粉砕効率に直接影響する。
- 回転数が低すぎると、ボールが十分に持ち上がらず、大きな衝撃を与えることができないため、粉砕効率が低下する。
- 回転数が高すぎると、ボールが遠心分離してミルの壁に付着し、粉砕作用が低下する。
- 臨界速度はボールが遠心分離を始める速度です。
-
適切な粉砕媒体の選択
- ボールの大きさ、密度、数は粉砕性能に大きく影響する。
- 微粉砕には小さいボールが適しており、粗粉砕には大きいボールが効果的である。
- ボールの密度は、粉砕する材料に合わせる必要があり、密度の高い材料には密度の高いボールが必要です。
- 衝撃を最大化し、摩耗を最小化するために、ボールと材料の比率を適切なものにする。
-
充填率のコントロール
- 充填率とは、粉砕機容積に占める粉砕媒体の割合のことです。
- 最適な充填率(通常30~40%)は、粉砕機に過負荷をかけることなく十分な粉砕作用を保証します。
- 過充填は粉砕効率を低下させ、過充填は十分な衝撃と摩耗をもたらします。
-
L:D比の調整
- ドラムの長さ(L)と直径(D)の比率は、粉砕機内での原料の滞留時間に影響します。
- 最適なL:D比(1.56~1.64)は、過剰なエネルギーを消費することなく効率的な粉砕を可能にします。
- ドラムを長くすると滞留時間が長くなり、微粉砕には有利ですが、処理能力が低下する可能性があります。
-
供給速度と原料特性の管理
- 供給速度はミルの粉砕能力とのバランスをとる必要があります。
- 原料の過負荷は、粉砕効率を低下させ、エネルギー消費量を増加させる。
- 供給原料の物理化学的特性(硬度、含水率など)も粉砕性能に影響する。原料の特性に応じた調整が必要な場合もある。
-
粉砕された製品を適時に除去
- 粉砕物の効率的な排出は、過粉砕を防ぎ、安定した製品品質を保証する。
- 材料と希望する細かさに応じて、適切な排出機構(火格子排出、オーバーフロー排出など)を使用する。
- 最適な性能を維持するために、排出システムを定期的に監視および調整する。
-
アーマ表面形状の維持
- ミルのアーマー(ライニング)の形状と状態は、粉砕効率と摩耗に影響する。
- 滑らかなライニングは微粉砕に適し、リブやウェーブのあるライニングは粗粉砕に適している。
- 摩耗したライニングは定期的に点検・交換し、粉砕効率を維持する。
-
粉砕の細かさの監視と管理
- 望ましい粉砕品の細かさは、粉砕パラメーターに影響します。
- 粒子を細かくするには、粉砕時間を長くし、ボールを小さくする必要があります。
- 粒度分析を使って細かさをモニターし、必要に応じてパラメータを調整します。
これらの要因に体系的に対処することで、ボールミルの生産量と効率を大幅に向上させることができます。各パラメーターは、最良の結果を得るために、特定の材料と操作要件に基づいて慎重に最適化されるべきである。
総括表
ファクター | 最適化のヒント |
---|---|
回転速度 | 最適な粉砕効率を得るために、臨界速度の65~75%を維持する。 |
粉砕媒体 | 微粉砕には小さいボール、粗粉砕には大きいボールを使用する。ボールの密度を材料に合わせます。 |
充填率 | 過充填や過少充填を避けるため、充填率を30~40%に保つ。 |
L:D比 | ドラムの長さと直径の比率(1.56~1.64)を最適化することにより、効率的な粉砕を実現します。 |
供給量と材料 | 供給量と粉砕能力のバランスをとり、材料の硬さと水分を調整する。 |
粉砕物の除去 | 過研磨を防ぐため、適切な排出機構を使用する。 |
アーマー表面形状 | 微粉砕には滑らかなライニング、粗粉砕にはリブ/ウェーブライニングをお選びください。 |
粉砕の細かさ | 粒子径をモニターし、粉砕パラメータを調整することで、ご希望の細かさに仕上げます。 |
ボールミル製造の最適化 当社の専門家にご連絡ください。 オーダーメイドのソリューションを