ふるい分けの有効性は、ふるい分けする材料の特性、ふるい分けパラメータ(時間、振幅、速度など)、ふるい分け機と材料や用途との適合性など、いくつかの要因に影響されます。粒子径、凝集傾向、静電気などの材料特性は、ふるい分け効率を決定する上で重要な役割を果たします。さらに、規格やガイドラインの遵守、機械の充填能力も最適な結果を得るために重要です。これらの要素を理解することは、効率的なふるい分けを行うための適切な機器とパラメーターの選択に役立ちます。
主なポイントを説明します:
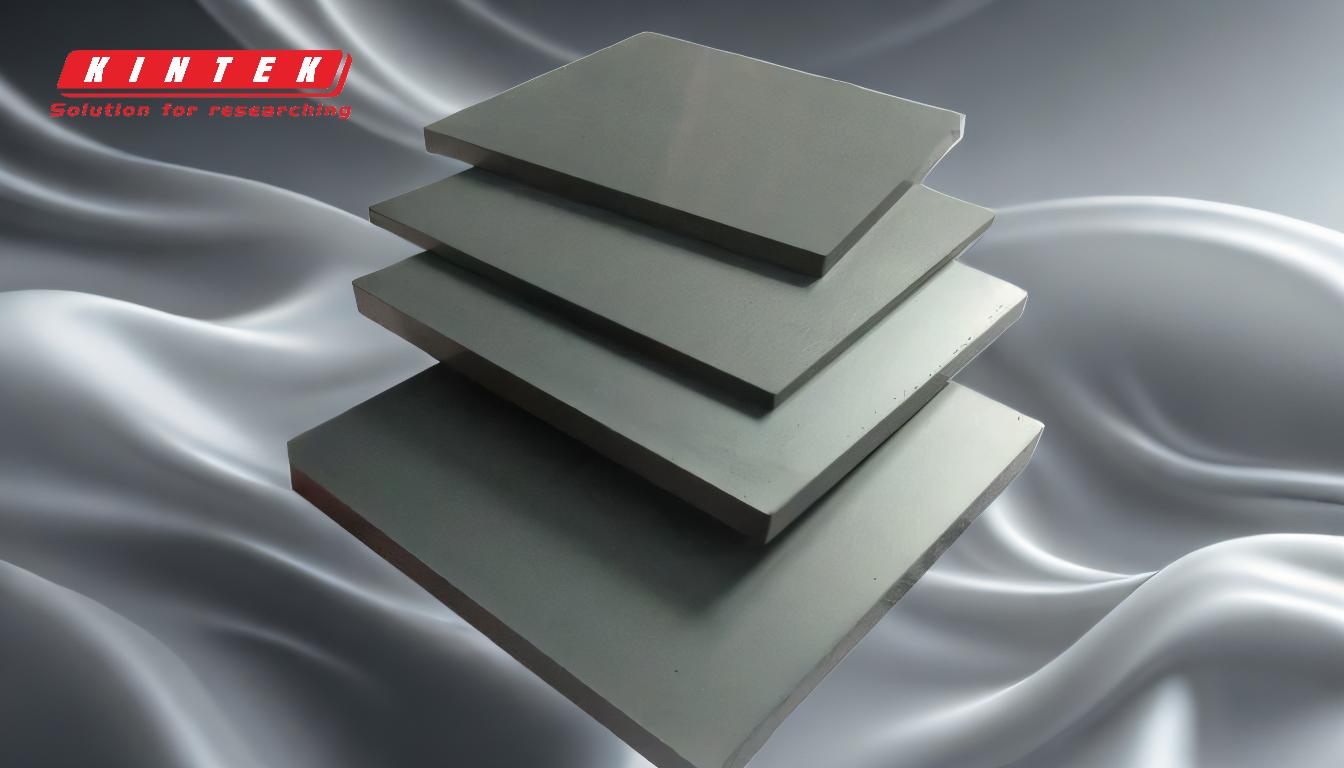
-
材料の特性
- 粒子サイズ:分離する粒子の最小サイズは、ふるい分け効果に直接影響します。粒子が小さいほど、メッシュサイズを細かくし、ふるい時間を長くする必要があります。
- 凝集:凝集しやすい材料は、ふるい分けの妨げになります。凝集を抑えるために帯電防止剤や前処理が必要な場合があります。
- 静電気:静電気を発生する材料は、ふるいメッシュに粒子を付着させ、効率を低下させます。静電気対策や湿度管理が必要な場合があります。
-
ふるい分けパラメータ
- ふるい時間:ふるい分け時間は、原料に応じて最適化する必要があります。時間が短すぎると分離が不完全になり、長すぎると装置が不必要に摩耗します。
- 振幅/速度:ふるい振とう機の振動の強さは、材料に合わせて調整する必要があります。振幅や速度が大きすぎるとデリケートな粒子を損傷する可能性があり、強さが不十分だと粒子を効果的に分離できない可能性があります。
- 規格とガイドライン:国内規格、国際規格、社内規格には、ふるい分けパラメータに関する具体的な推奨事項が定められています。これらに従うことで、結果の一貫性と正確性が保証されます。
-
機械の互換性
- 充填容量:ふるい機は、用途に応じた必要容量に合わせる必要があります。過負荷はふるい効率を低下させ、過負荷はふるいムラの原因となります。
- 装置の互換性:ふるい機は、原料の性質とふるい分け結果に適合したものでなければなりません。例えば、湿式ふるい分けには乾式ふるい分けとは異なる機械が必要な場合があります。
-
環境要因と運転要因
- 湿度と温度:環境条件:環境条件は、凝集や静電気などの材料特性に影響を与えます。環境条件をコントロールすることで、ふるい分け効率を向上させることができます。
- メンテナンスとキャリブレーション:ふるい機の定期的なメンテナンスと校正により、安定した性能と正確な結果が得られます。
これらの要素を考慮することで、機器や消耗品の購入者は、それぞれの用途に最適な結果を得るために、適切なふるい分け機器とパラメータを選択することができます。
総括表
ファクター | 主な考慮事項 |
---|---|
材料の特性 | - 粒子径:メッシュサイズとふるい分け時間に影響します。 |
- 凝集:帯電防止剤または前処理が必要な場合がある。 | |
- 静電気:湿度管理または帯電防止対策が必要。 | |
ふるい分けパラメータ | - 時間装置を過負荷にすることなく完全に分離するよう最適化します。 |
- 振幅/速度:粒子の損傷や非効率的な分離を避けるために調整します。 | |
- 標準:一貫性を保つため、国内外のガイドラインに従う。 | |
機械の互換性 | - 充填能力:機械の能力をアプリケーションのニーズに合わせます。 |
- 装置の互換性:湿式または乾式ふるい分けに適していることを確認する。 | |
環境要因 | - 湿度/温度:凝集や静電気の問題を軽減するためのコントロール。 |
- メンテナンス定期的な校正により、安定した性能を発揮します。 |
ふるい分けプロセスの最適化 当社の専門家にご連絡ください。 オーダーメイドのソリューションを