ロータリーエバポレーション(ロトバップ)と一般的な蒸留は、どちらも混合物の成分を分離するために使用される技術ですが、そのメカニズム、用途、結果は大きく異なります。ロトバップは減圧下で行われるため、沸点が低く、化合物の分離が穏やかで、食品フレーバーやエッセンスのようなデリケートな物質に最適である。これとは対照的に、標準的な蒸留は高温を伴うことが多く、繊細な化合物を変質させたり劣化させたりする可能性がある。また、標準的な蒸留が残渣よりも蒸留液の回収に重点を置くのに対し、Rotovapは表面積の増大と連続的な攪拌により、より速く効率的な蒸留が可能である。
キーポイントの説明
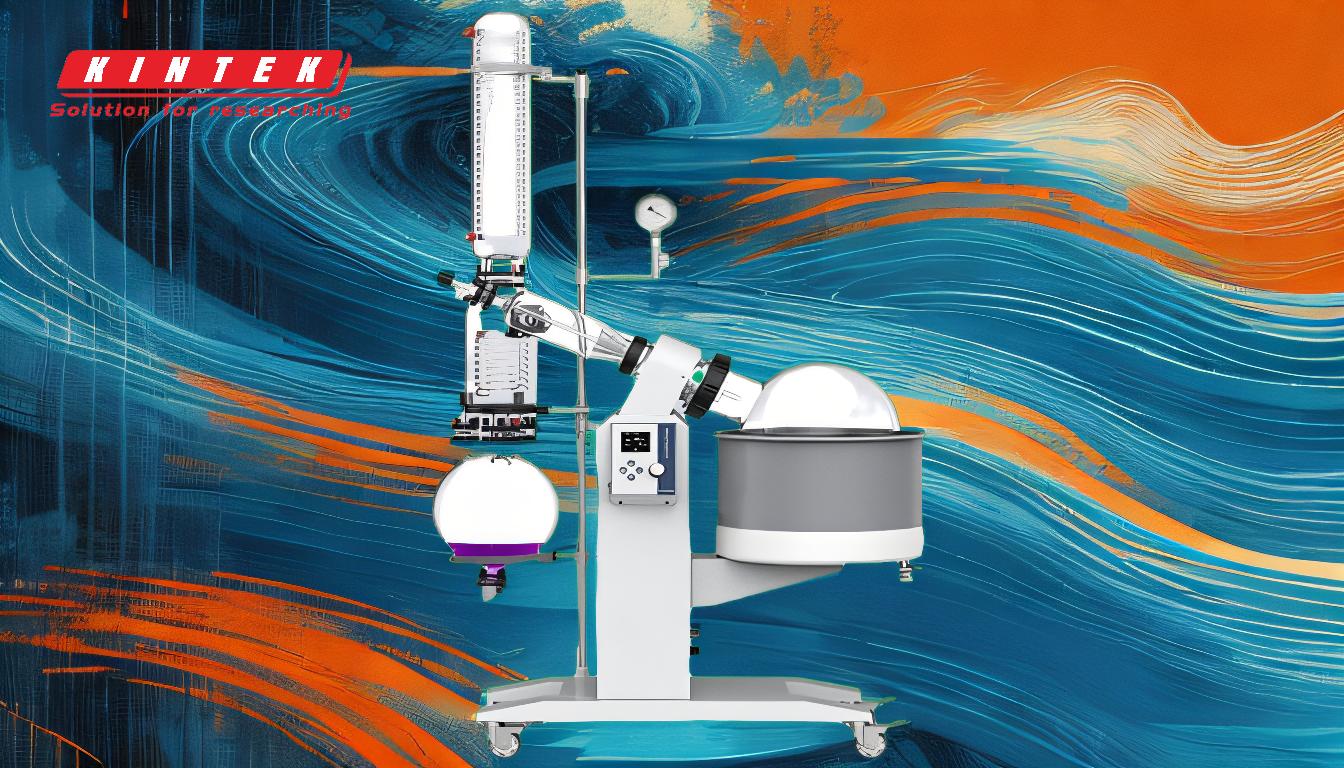
-
温度管理と圧力:
- ロトバップ:真空条件下で作動するため、溶剤の沸点が大幅に下がります。これにより、より低い温度での蒸留が可能になり、フレーバーやエッセンス、その他のデリケートな物質のような熱に弱い化合物の完全性を保つことができます。
- 標準蒸留:通常、大気圧で作動するため、沸騰させるためには高温が必要となる。このため、デリケートな化合物の熱劣化や変質につながる可能性があり、デリケートな材料には適さない。
-
分離のメカニズム:
- ロトバップ:フラスコが回転することで、混合物の表面積が増加し、より速く均一な蒸発が促進されます。真空により、溶媒はより低い温度で蒸発し、システムは溶媒をほぼ100%回収するように設計されている。残渣(濃縮された化合物)は元のフラスコに残る。
- 標準蒸留:混合物を加熱して沸騰させ、蒸気を凝縮させる。蒸留物(回収された溶剤)が主な生成物であり、溶剤の回収や熱に弱い化合物の保存には効率が悪い。
-
用途:
- ロトバップ:食品、飲料、製薬業界など、デリケートな化合物の保存を必要とする用途に最適。液体と固体の分離、タンニンの除去、色や苦味のような好ましくない成分の除去が可能で、風味のプロファイルは完全に保持されます。
- 標準蒸留:石油精製やアルコール製造など、化合物の熱安定性が問題にならない産業でよく使用される。熱に弱い物質の保存を必要とする用途にはあまり適していない。
-
効率とスピード:
- ロトバップ:真空、回転、表面積の増加の組み合わせにより、プロセスがより速く効率的になります。連続的な混合は、均一な加熱と蒸発を保証し、局所的な過熱のリスクを低減します。
- 標準蒸留:特に溶剤の回収やデリケートな化合物の分離に適している。このプロセスは時間がかかり、高いエネルギー投入を必要とする場合がある。
-
プロセスの結果:
- ロトバップ:残渣(濃縮された化合物)を元のフラスコ内に保持することに重点を置き、溶液を濃縮したり、特定の化合物をその性質を変えることなく単離するのに適しています。
- 標準蒸留:蒸留物(溶媒)を主な製品として回収することに重点を置いているため、残渣が目的の用途には適さない場合がある。
-
精度とコントロール:
- ロトバップ:温度、圧力、回転速度など、蒸留プロセスを正確に制御します。これにより、成分分離を調整することができ、敏感な化合物を損傷するリスクを最小限に抑えることができます。
- 標準蒸留:特に温度と圧力の面で、プロセスのコントロールが難しくなり、特にデリケートな素材の場合、結果が予測しにくくなる可能性がある。
要約すると、ロトバップはより高度で特殊な蒸留の形態であり、デリケートな化合物の穏やかな分離と保存を必要とする用途向けに設計されている。標準的な蒸留は、多くの工業プロセスに有効であるが、熱に敏感な物質に必要な精度と優しさに欠ける。両者の選択は、分離される化合物の性質や望ましい結果を含む、アプリケーションの特定の要件に依存する。
要約表
側面 | ロータリーエバポレーション | 標準蒸留 |
---|---|---|
温度と圧力 | 真空下で使用することで、沸点を下げ、熱に弱い化合物を保存することができます。 | 大気圧下で作動するため、高温が要求され、熱劣化の危険性がある。 |
メカニズム | フラスコを回転させることで表面積を増やし、真空にすることで溶媒を効率よく回収する。 | 沸騰まで加熱し、凝縮させる。 |
用途 | 食品、飲料、製薬業界のデリケートな化合物に最適。 | 石油精製やアルコール製造などの産業で使用されています。 |
効率とスピード | 真空、回転、表面積の増加により、より速く効率的。 | 特にデリケートな化合物の場合、速度が遅く、効率が悪い。 |
結果 | 残渣(濃縮された化合物)をフラスコ内に保持することに重点を置く。 | 主生成物である蒸留物(溶媒)の回収に重点を置く。 |
精度と制御 | 温度、圧力、回転速度を正確に制御。 | 制御性が低いため、繊細な材料では結果が予測しにくい。 |
お客様の用途に適した蒸留方法の選択にお困りですか? 当社の専門家にご相談ください!