研削は、ワークピースから不要な材料を除去し、所望の幾何学的・寸法的精度、表面仕上げ、表面の完全性を達成するために使用される精密機械加工プロセスである。金属、セラミック、ガラス、炭化物などの材料を切断、成形、仕上げするために、砥石やその他の工具の形で結合した砥粒を使用します。このプロセスでは、さまざまな粒子径のものを作ることができ、粒子が細かいほど加工時間が長くなる。粉砕はまた、表面積の増加、特定の粒径の達成、さらなる加工のための材料の準備といった目的もある。このプロセスには、原料の供給、粉砕、粒径の縮小、不純物の分離といったステップが含まれる。
主なポイントを説明します:
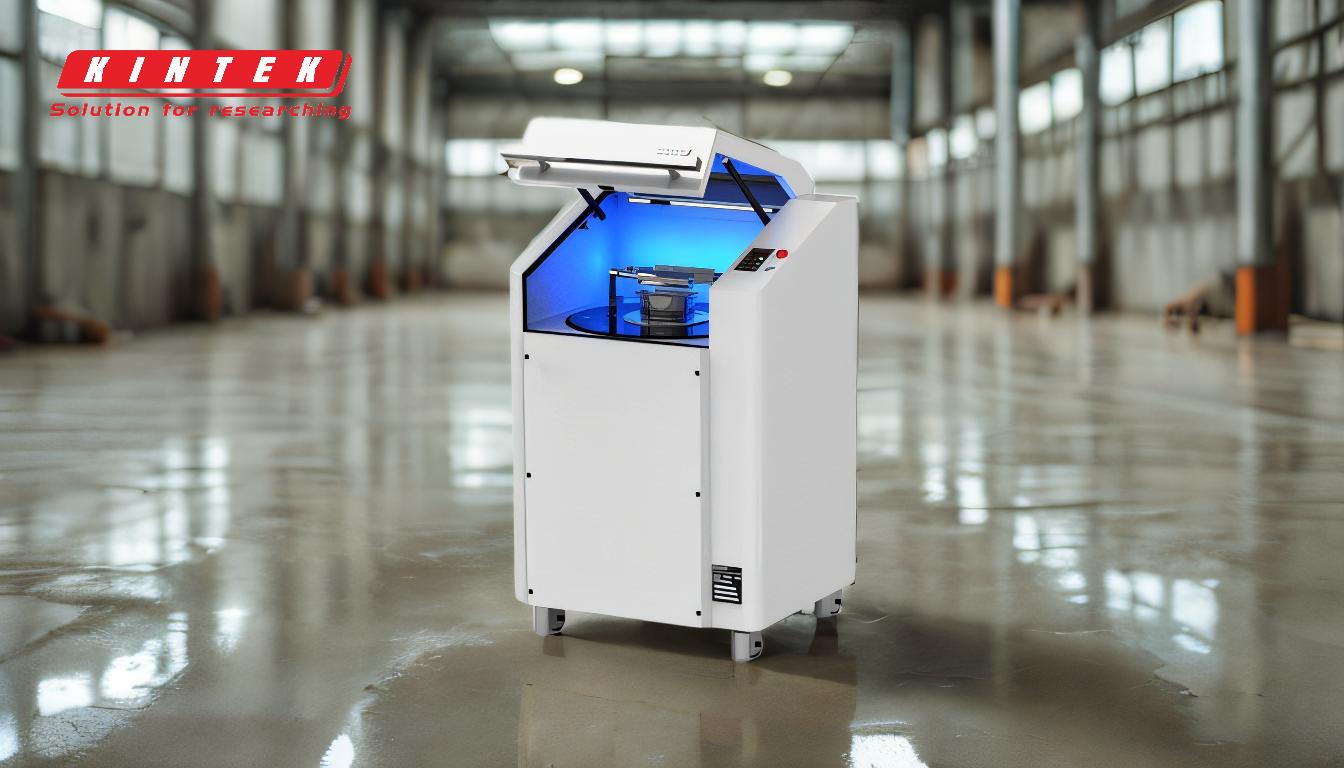
-
研磨の目的:
- 材料除去:研削は、表面から不要な材料やバルクストックを除去し、工作物を成形し、仕上げます。
- 表面仕上げと完全性:高品質の表面仕上げを保証し、材料の構造的完全性を維持します。
- 寸法精度:研削加工は、エンジニアリング用途で重要な精密な幾何学的公差と寸法公差を実現します。
-
研削加工力学:
- 研磨作用:砥石に埋め込まれた砥粒(炭化ケイ素、酸化アルミニウムなど)を利用して、材料を切断または成形するプロセス。
- 材料の供給:ワークが研削盤に投入され、回転する砥石に接触する。
- 切り屑の形成:研磨粒子がワークピースと相互作用する際に、チップの形で材料を除去し、表面を磨き上げます。
-
粒度制御:
- メッシュサイズ:粉砕工程では10~40メッシュの粒子を作ることができ、粒子が細かいほど処理時間が長くなる。
- 複数の粉砕:より小さな粒子径を得るためには、複数回の粉砕サイクルを採用することができるが、実用的な下限は40メッシュ程度である。
- 歩留まり:プロセスの歩留まりは所望の粒子径によって異なり、粗い粒子では歩留まりが高く(例えば、10~20メッシュで毎時2,000~2,200ポンド)、細かい粒子では歩留まりが低くなる(例えば、30~40メッシュで毎時1,200ポンド)。
-
不純物の分離:
- 空気分離:エア分離またはエアテーブルを使用して繊維や異物を除去し、最終製品のクリーン度を確保します。
- 磁気分離:磁選機で金属不純物を除去し、さらに精製します。
-
研磨の用途:
- 表面積増加:粉砕は固体の表面積を増加させ、化学反応やコーティングのようなプロセスで有用です。
- 粒度コントロール:セラミックスや冶金などの産業で不可欠な、特定の粒径の固形物を製造するために使用される。
- 資源パルプ化:粉砕は、紙・パルプ産業におけるパルプ化など、さらなる加工のために材料を準備します。
-
粉砕の種類:
- 平面研削:工作物に平らな面を作るために使用される。
- 円筒研削:シャフトやロッドの製造によく使用される。
- センタレス研削:工作物を刃物で支え、2つの砥石の間で回転させる工程で、大量生産に最適。
- 工具研削:切削工具を研ぎ、維持するために使用される。
-
研削効率を左右する要因:
- ホイールスピード:砥石速度を上げると、材料除去率が向上するが、発熱が大きくなる可能性がある。
- 送り速度:工作物を砥石に送り込む速度は、仕上がりと精度に影響します。
- クーラントの使用:クーラントは、発熱を抑え、ワークへの熱損傷を防ぐために使用されることが多い。
-
研削の利点:
- 精密:研削は高い精度と正確さを提供し、重要な用途に適しています。
- 汎用性:硬いもの、脆いものなど、幅広い素材に使用できる。
- 表面品質:このプロセスは、しばしば高性能部品に要求される優れた表面仕上げを実現する。
-
研削への挑戦:
- 発熱:過度の熱は加工物に熱損傷を与える可能性があるため、クーラントを使用する必要がある。
- ホイールの摩耗:研削砥石は時間の経過とともに磨耗し、定期的なドレッシングまたは交換が必要になります。
- コスト:特殊な設備や消耗品が必要なため、コストが高くなる可能性がある。
-
研削加工の今後の動向:
- オートメーション:より高い効率性と一貫性を実現するために、自動研削システムの利用が増加している。
- 先端材料:性能向上のための新しい研磨材と接合技術の開発。
- 持続可能性:研削加工における無駄とエネルギー消費の削減に焦点を当てる。
要約すると、研削は様々な材料の高品質な仕上げと寸法精度を達成するために不可欠な、多用途で精密な機械加工プロセスである。その用途は様々な産業に及び、技術の進歩はその効率性と持続可能性を高め続けている。
総括表
アスペクト | 詳細 |
---|---|
目的 | 材料除去、表面仕上げ、寸法精度 |
プロセス力学 | 研磨作用、材料供給、切り屑形成 |
粒度制御 | 10~40メッシュの範囲、より微細な粒子のための複数粉砕 |
不純物分離 | 空気分離、磁気分離 |
用途 | 表面積増大、粒度調整、資源パルプ化 |
研削の種類 | 平面研削、円筒研削、センタレス研削、工具研削、カッター研削 |
能率要因 | ホイール速度、送り速度、クーラント使用量 |
利点 | 精度、汎用性、優れた表面品質 |
課題 | 発熱、ホイール摩耗、コスト |
今後の動向 | 自動化、先端材料、持続可能性 |
研削が製造工程をどのように向上させるかをご覧ください。 今すぐお問い合わせください !