スパッタリングとメッキは、どちらも基板上に薄膜を成膜するために用いられる技術であるが、そのメカニズム、プロセス、用途は大きく異なる。スパッタリングは物理的気相成長法(PVD)の一種で、ターゲット材料に高エネルギーのイオンをぶつけて原子を放出させ、その原子が基板上に堆積する。対照的に、メッキは通常、溶液中の金属イオンを還元して基板上に析出させる電気化学的プロセスを伴う。スパッタリングはソース材料を溶かす必要がなく、高いガス圧で作動するが、めっきは化学反応に依存し、多くの場合液体媒体を必要とする。どちらの方法もエレクトロニクス、光学、コーティングなどの産業で使用されているが、その選択はアプリケーションの特定の要件に依存する。
キーポイントの説明
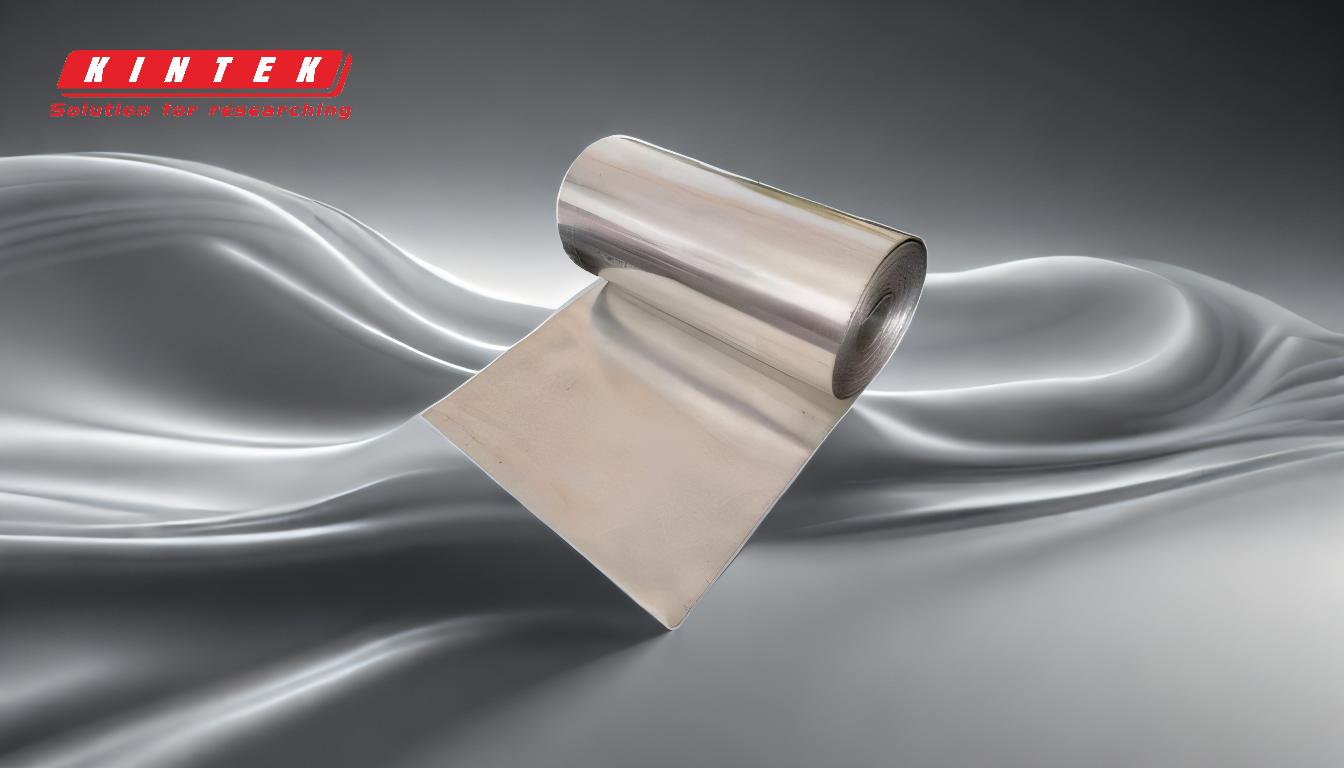
-
成膜のメカニズム:
- スパッタリング:高エネルギーイオン(通常はプラズマから)を用いてターゲット材料に衝突させ、運動量移動によって原子をターゲットから放出させる。放出された原子は移動し、基板上に堆積して薄膜を形成する。このプロセスでは、ターゲット材料が溶融する必要はない。
- メッキ:通常、電気化学的プロセスに依存する。溶液中の金属イオンが基板表面で還元され、金属皮膜が形成される。このプロセスでは、還元反応を促進するために電流が使用されることが多い。
-
プロセス環境:
- スパッタリング:不活性ガス(アルゴンなど)を使用した真空または低圧環境で動作する。スパッタ粒子は基板に到達する前に気相衝突を起こす可能性がある。
- めっき:通常、液体媒体(電解質溶液)中で行われる。基板を溶液に浸し、電気化学反応によって金属イオンを表面に析出させる。
-
エネルギー源:
- スパッタリング:電気エネルギーを使ってプラズマを発生させ、ターゲット材料をスパッタするのに必要な高エネルギーイオンを生成する。このプロセスは、熱エネルギーではなく、物理的な衝突によって駆動される。
- メッキ:溶液中の金属イオンの還元を電気エネルギーに頼る。このエネルギーは、基板上に金属を析出させる化学反応を促進するために使用される。
-
蒸着速度と制御:
- スパッタリング:一般的に、熱蒸発法など他のPVD法に比べて成膜速度が低い。しかし、膜の組成や均一性のコントロールに優れているため、精密な用途に適している。
- めっき:特に電気めっきプロセスにおいて、高い析出速度を達成できる。皮膜の厚さと均一性は、電流密度やめっき時間などのパラメーターを調整することで制御できる。
-
材料適合性:
- スパッタリング:金属、合金、セラミックスなど幅広い材料を蒸着できる。特に融点が高く蒸発しにくい材料に有効。
- メッキ:主に金属や合金の析出に用いられる。このプロセスは、電解質溶液に溶解し、基板上に還元できる材料に限定される。
-
応用例:
- スパッタリング:半導体産業、光学コーティング、薄膜太陽電池でよく使われる。また、工具用の硬質コーティングや装飾用コーティングにも使用される。
- メッキ:自動車(耐食性)、エレクトロニクス(導電層)、宝飾品(装飾仕上げ)などの産業で広く使用されている。
-
利点と限界:
-
スパッタリング:
- 利点高精度、複雑な材料の蒸着能力、良好な接着性、均一性。
- 制限事項蒸着速度の低下、設備コストの上昇、真空環境の必要性。
-
メッキ:
- 利点高い成膜速度、大量生産におけるコスト効率、複雑な形状へのコーティング能力。
- 限界:導電性基板への限定、化学廃棄物による環境問題の可能性、スパッタリングに比べ膜組成の制御が難しい。
-
スパッタリング:
まとめると、スパッタリングとメッキは、独自のメカニズム、環境、用途を持つ別個の成膜技術である。スパッタリングは精度と材料の多様性に優れ、めっきはその速度と大規模な金属蒸着における費用対効果で支持されている。両者の選択は、所望の材料特性、蒸着速度、基板の特性など、用途の具体的な要件によって決まる。
総括表
側面 | スパッタリング | メッキ |
---|---|---|
メカニズム | 高エネルギーイオンを使用してターゲット原子を放出する物理蒸着(PVD)。 | 溶液中の金属イオンを電気化学的に還元する方法。 |
環境 | 真空または不活性ガスによる低圧。 | 液体媒体(電解質溶液)。 |
エネルギー源 | プラズマを発生させるための電気エネルギー | 還元反応を促進する電気エネルギー |
蒸着速度 | 低レート、高精度。 | 高いレート、大規模生産に適しています。 |
材料適合性 | 金属、合金、セラミック | 主に金属と合金 |
用途 | 半導体、光学コーティング、太陽電池 | 自動車、電子機器、宝飾品 |
利点 | 高精度、材料の多様性、良好な接着性。 | 成膜速度が速く、大量生産に適している。 |
制限事項 | 蒸着率が低い、装置コストが高い、真空が必要。 | 導電性基板に限定される、化学廃棄物による環境への懸念。 |
適切な蒸着技術の選択にお困りですか? 当社の専門家に今すぐご連絡ください にお問い合わせください!