ふるい分け方法は、その精度と効率を決定するいくつかの要因に影響されます。これらの要因には、粒子径、凝集しにくさ、静電気の影響を受けやすさなど、ふるいにかける材料の特性が含まれます。湿度などの環境条件も重要な役割を果たします。乾燥した状態では、静電気によって粒子がふるいに付着する可能性があるからです。さらに、信頼性の高い結果を得るためには、ふるいの動きや機械の充填能力など、ふるい分け装置の設計と操作が重要です。これらの要素を理解することで、特定の用途に適したふるい分け方法と装置を選択することができます。
主なポイントを説明します:
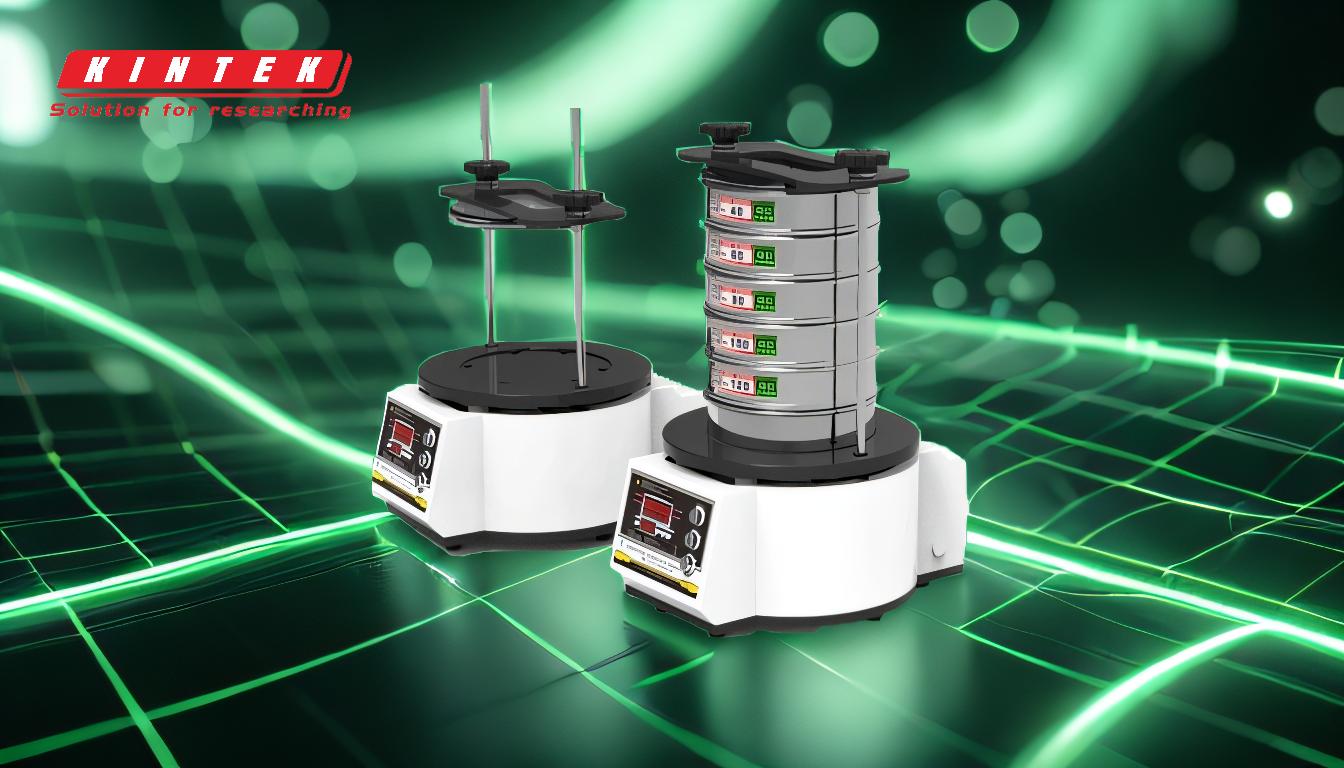
-
材料の特性:
- 粒子径:分離する粒子の最小サイズが重要です。小さな粒子はより細かいメッシュのふるいを必要とし、大きな粒子はより粗いメッシュを必要とします。
- 凝集に対する耐性:凝集しやすい材料は、ふるい分けプロセスの妨げになります。適切な前処理や凝集防止剤の使用が必要な場合があります。
- 静電気:静電気を帯びやすい材料は、粒子がふるいや粒 子同士に付着し、ふるい工程の効率を低下させま す。特に乾燥した環境で問題となります。
-
環境条件:
- 湿度:湿度が高いと静電気が発生しにくくなり、微粉をふるいやすくなります。逆に湿度が低いと静電気が増加し、粒子がふるいに付着しやすくなります。
- 温度:極端な高温は、材料の特性やふるい分けプロセスに影響を与えます。例えば、高温になると材料がしなやかになったり、粘着性が増したりします。
-
ふるい装置の設計と操作:
- ふるい動作:ふるいの効果は、ふるいの動きによって決まります。垂直または水平に動くことで、粒子が十分に攪拌され、小さな粒子はメッシュを通過し、大きな粒子は表面に残ります。
- 充填能力:ふるい振とう機に投入する原料の量は、ふるい振とう機の能力に合わせてください。充填量が多すぎると効率が悪くなり、逆に充填量が少ないと正確な分離ができません。
- 互換性:ふるい振とう機は、原料や用途に適合したものでなければなりません。これには、ふるいメッシュの種類、ふるいサイズ、機械の全体的な設計などが含まれます。
-
材料の前処理:
- 乾燥または加湿:材料や環境条件によっては、ふるい分けプロセスを最適化するために乾燥や加湿などの前処理が必要な場合があります。
- 脱凝集:凝集しやすい材料の場合、ふるい分け前に機械的または化学的な脱凝集法を採用して、粒度分布をより均一にすることができます。
-
機器のメンテナンスと校正:
- 定期的なメンテナンス:ふるい振とう機の性能を安定させるには、ふるい振とう機を常に良好な状態に保つことが重要です。これには、ふるいの洗浄、摩耗や損傷のチェック、破損した部品の交換などが含まれます。
- キャリブレーション:ふるい機を定期的に校正することで、ふるい機が指定されたパラメーター内で作動し、正確で信頼性の高い結果が得られるようになります。
これらの要素を考慮することで、ふるい分けプロセスを最適化し、粒径に基づく正確で効率的な分離を実現できます。これは、医薬品、食品加工、建設資材など、正確な粒度分布が重要な産業において特に重要です。
総括表
要因 | 主な考慮事項 |
---|---|
材料特性 | - 粒子径:より細かいか粗いメッシュが必要。 |
- 凝集に対する耐性:前処理が必要な場合がある。 | |
- 静電気:乾燥状態だと粒子が付着することがある。 | |
環境条件 | - 湿度: 湿度が高いと静電気が減少し、低いと増加する。 |
- 温度:極端な温度は材料特性に影響を与えます。 | |
装置設計 | - ふるいの動き:垂直または水平攪拌により分離が向上します。 |
- 充填容量:過負荷または過少負荷は効率を低下させます。 | |
- 互換性:材料とアプリケーションのニーズに合わせて装置を選択します。 | |
前処理 | - 乾燥または加湿:最適なふるい分けができるように原料の水分を調整します。 |
- 脱凝集:粒度分布を均一にします。 | |
メンテナンス | - 定期的な洗浄と校正により、安定した性能を保証します。 |
ふるい分けプロセスの最適化についてお困りですか? 当社の専門家にご相談ください。 お問い合わせください!