スパッタリングは広く使われている薄膜蒸着技術であるが、いくつかの顕著な欠点がある。これには、高い設備投資、特定の材料では比較的低い蒸着率、膜汚染のしやすさ、膜厚制御の難しさなどがある。さらに、スパッタリングはイオン衝撃によって有機固体のような敏感な材料を劣化させる可能性があり、複雑な装置とメンテナンスを必要とする。このプロセスはまた、材料の選択やリフトオフプロセスのような他の技術との統合にも限界がある。このような欠点があるため、スパッタリングは特定の用途、特に精度、コスト効率、材料適合性が重要な用途には適していない。
要点の説明
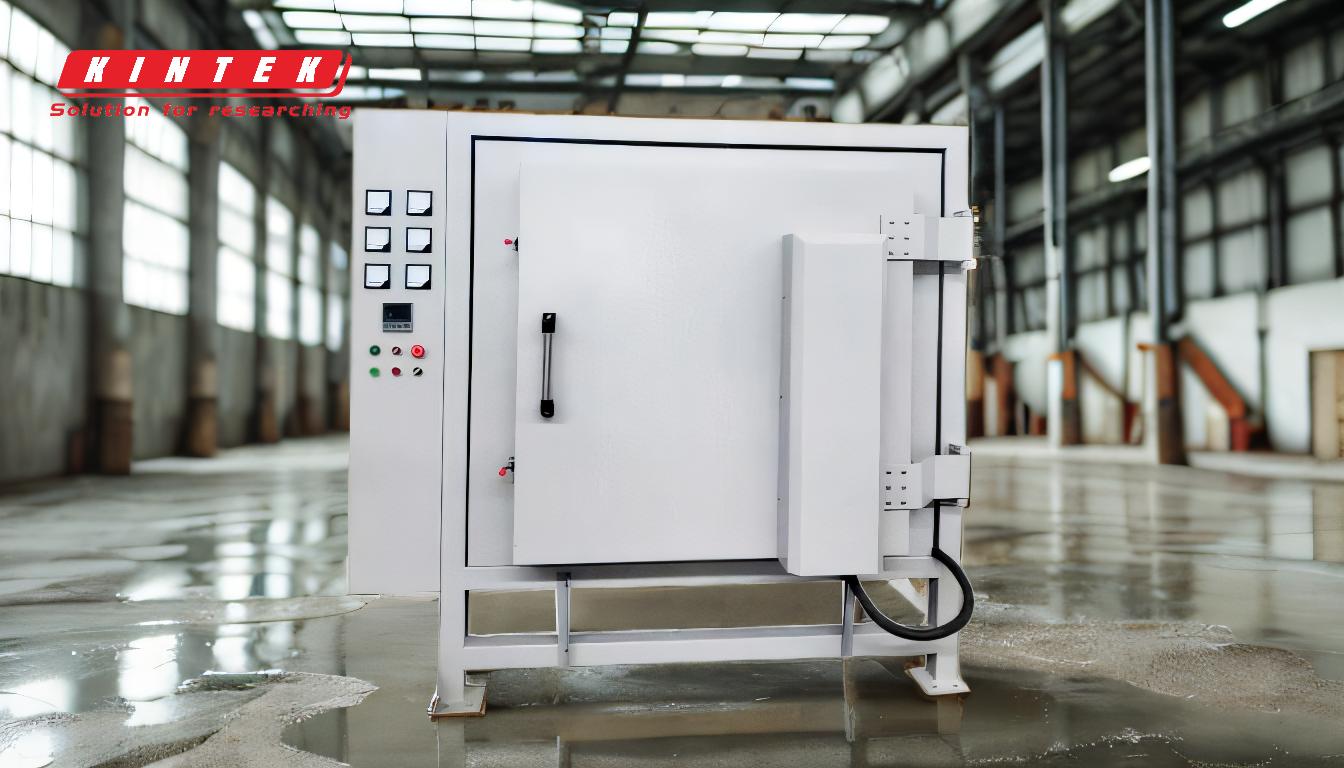
-
高額な設備投資:
- スパッタリング装置は複雑で、高圧装置や真空システムに多額の投資を必要とする。このため、初期セットアップにコストがかかり、小規模な事業や研究所にとっては障壁となりうる。
-
低い蒸着率:
- SiO2のような特定の材料では、スパッタリングでの成膜速度は、蒸発法のような他の技術に比べて相対的に低い。このため、処理時間が長くなり、スループットが低下し、全体的な効率に影響を及ぼす可能性がある。
-
フィルム汚染:
- スパッタリングは、蒸着に比べ、基板に不純物を導入する傾向が強い。これは、スパッタリングがより低い真空範囲で動作するため、ソース材料やスパッタリングガスからの不純物が膜中に拡散するためである。
-
材料の劣化:
- 一部の材料、特に有機固体は、スパッタリングプロセス中のイオン衝撃によって劣化しやすい。このため、この技法で効果的に成膜できる材料の範囲が制限される。
-
基板温度上昇:
- スパッタリング工程は、基板温度の大幅な上昇を引き起こす可能性があり、温度に敏感な材料や基板に悪影響を及ぼす可能性がある。このため、冷却システムを追加する必要があり、エネルギーコストが増加し、生産率が低下する。
-
膜厚制御の難しさ:
- スパッタリングでは、膜厚を正確に制御することが難しい。これは、高度に均一な、あるいは特殊な膜特性を必要とする用途では、致命的な制限となりうる。
-
リフトオフ・プロセスにおける統合の課題:
- スパッタリングは、膜の構造化に用いられるリフトオフプロセスとの組み合わせが難しい。スパッタリングの特徴である拡散輸送は、完全なシャドウイングを不可能にし、コンタミネーションの問題につながり、パターン化された膜の製造を複雑にする。
-
材料選択の限界:
- スパッタリングにおけるコーティング材料の選択は、その融点によって制限される。高融点材料はスパッタリングに適さない場合があり、応用範囲が制限される。
-
メンテナンスと運用の複雑さ:
- スパッタリングシステムは、定期的なメンテナンスとプロセスパラメーターの慎重な管理を必要とする。このため、運転が複雑化し、ダウンタイムが発生し、生産性に影響を及ぼす可能性がある。
-
スパッタリングガスからの不純物導入:
- アルゴンなどの不活性スパッタリングガスは、成長膜中の不純物となる可能性がある。これは、半導体製造のような高純度膜を必要とする用途では特に問題となる。
まとめると、スパッタリングは多用途で広く使用されている成膜技法であるが、その欠点は、高コスト、低成膜速度、汚染、材料劣化など多岐にわたり、特定の用途には適していない。これらの制限を理解することは、特定のプロジェクト要件に基づいて適切な蒸着法を選択する上で極めて重要である。
要約表
デメリット | デメリット |
---|---|
高額な設備投資 | 複雑な装置や真空システムには多額の初期投資が必要。 |
低い蒸着速度 | SiO2のような材料では、蒸着技術に比べて蒸着速度が遅い。 |
膜の汚染 | 真空度が低いため、不純物の影響を受けやすい。 |
材料の劣化 | 有機固体はイオン衝撃で分解し、材料の適合性を制限する。 |
基板の温度上昇 | 熱に敏感な材料は、追加の冷却システムが必要になる場合があります。 |
膜厚制御の難しさ | 正確で均一な膜厚を実現するための課題。 |
リフトオフプロセスとの融合 | 拡散輸送のため、リフトオフプロセスとの統合は難しい。 |
材料選択の制限 | 高融点材料はスパッタリングに適さない場合がある。 |
メンテナンスと操作の複雑さ | 定期的なメンテナンスとプロセスパラメーターの慎重な管理が必要。 |
ガスからの不純物混入 | アルゴンのような不活性ガスは、高純度フィルム中の不純物になる可能性があります。 |
適切な成膜技術の選択にお困りですか? 当社の専門家に今すぐご連絡ください お客様のプロジェクトに最適なソリューションをご提案いたします!