スパッタリングは薄膜成膜に広く用いられている技術であるが、その効率、コスト、成膜品質に影響するいくつかの顕著な限界がある。これらの限界には、膜の汚染、低い成膜速度、高いエネルギー消費、膜厚制御の困難さ、材料選択の課題などの問題が含まれる。さらに、特殊な装置やメンテナンスが必要なため、プロセスが高価になることもあり、あらゆる種類の材料や用途に適しているとは限りません。これらの限界を理解することは、スパッタリングプロセスを最適化し、特定のニーズに適した成膜方法を選択する上で極めて重要である。
キーポイントの説明
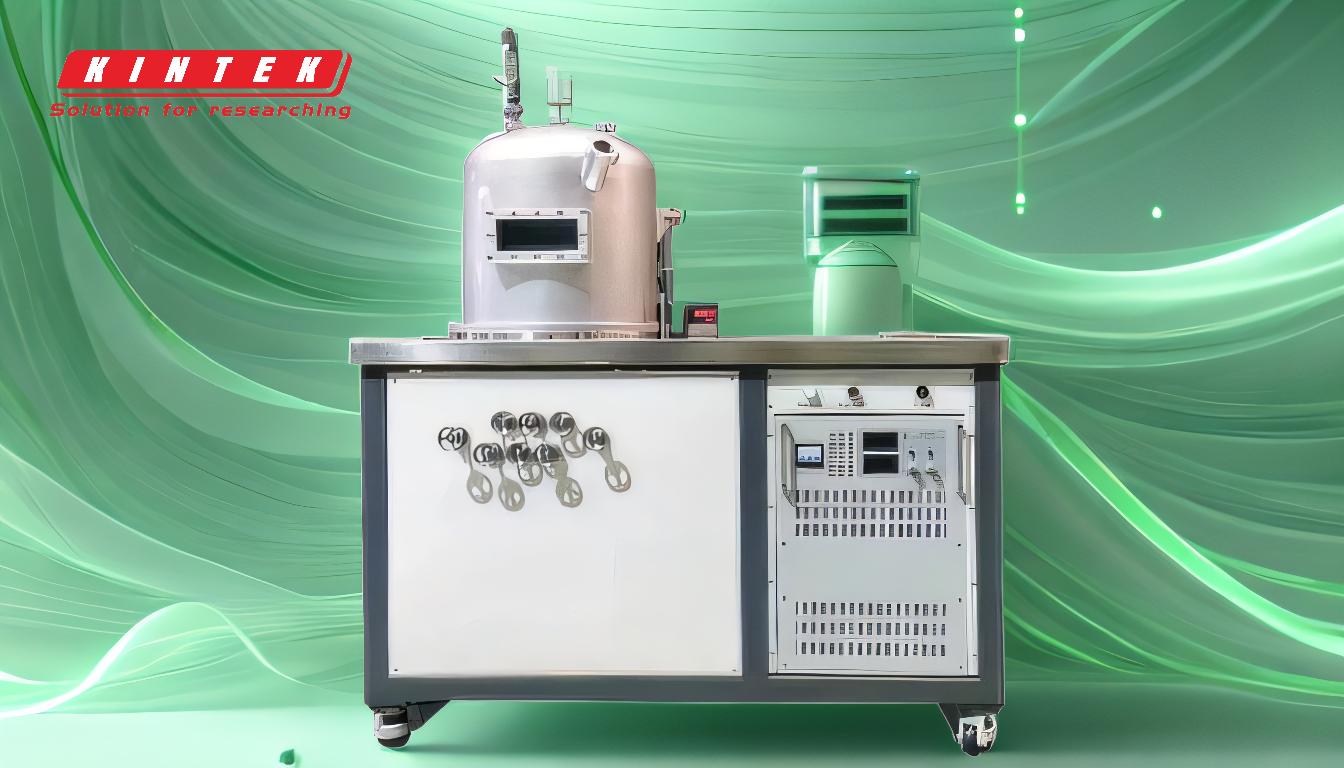
-
フィルム汚染:
- 原料からの不純物:スパッタリングプロセス中、ソース材料からの不純物が膜中に拡散し、汚染につながることがある。特に、ソース材料に揮発性不純物が含まれ、それが蒸発して基板上に堆積する場合に問題となる。
- ガス状汚染物質:スパッタリングで使用されるプラズマは、ガス状の汚染物質を活性化させる可能性があり、その汚染物質が成長するフィルムに取り込まれるため、汚染のリスクがさらに高まる。
- 不活性ガス不純物:アルゴンなどの不活性スパッタリングガスも、成膜チャンバーから効果的に除去されないと、膜中の不純物となる可能性がある。
-
低堆積率:
- 熱蒸発との比較:スパッタリングは一般に、熱蒸着技術に比べて成膜速度が低い。このため、処理時間が長くなり、高スループットの生産環境には適さない場合がある。
- 不均一な蒸着フラックス:スパッタされた原子の分布は不均一であることが多く、基板全体で均一な膜厚を得るためには、移動治具やその他の方法を使用する必要がある。
-
エネルギー消費と熱管理:
- 高いエネルギーコスト:ターゲットに入射するエネルギーの大部分は熱に変換され、装置の損傷を防ぎ、プロセスの安定性を維持するためには、この熱を効果的に除去する必要がある。このため、冷却システムを使用する必要があり、エネルギー消費と運転コストが増加する。
- 冷却システム要件:冷却システムの必要性は、エネルギー・コストを増加させるだけでなく、過熱を避けるためにシステムを定期的に冷却しなければならないため、全体的な生産率を低下させる。
-
フィルム厚のコントロール:
- レイヤーごとの成長の難しさ:スパッタリングは、パルスレーザー蒸着のような他の成膜方法と比較して、正確なレイヤー・バイ・レイヤー成長を達成するのに有効ではない。このため、特に複雑な多層構造では、膜厚を正確に制御することが難しくなります。
- スパッタされた原子の拡散輸送:スパッタリングされた原子輸送の拡散性により、リフトオフプロセスのような特定の膜構造化技術に必要な完全なシャドーイングを達成することが困難である。
-
材料の選択と目標コスト:
- 溶解温度に基づく制限:コーティング材料の選択は、融点によって制限されることが多い。融点が非常に高い材料はスパッタリングに適さない場合があり、高いエネルギー投入を必要とし、コンタミネーションのリスクが高まる可能性がある。
- 高価なターゲット:スパッタリングターゲットは高価であることが多く、スパッタされた材料がすべて基板上に堆積するわけではないため、材料の使用効率が悪いことがある。この非効率性により、プロセス全体のコストが上昇する。
-
プロセスパラメーターとメンテナンス:
- 高い動作圧力:従来のスパッタリング・プロセスは一般的に高圧で動作するため、エラストマー・シールへの浸透や安定した真空環境の維持が困難であるなどの問題が生じる可能性がある。
- ユーザーによるメンテナンス:スパッタリングプロセスには定期的なメンテナンスが必要だが、これには時間とコストがかかる。ユーザーによるメンテナンスの必要性は、操作の複雑さを増し、プロセスの全体的な効率に影響を与える可能性がある。
-
反応性スパッタリングの課題:
- ガス組成コントロール:反応性スパッタ蒸着では、ターゲット材料が反応性ガスと反応して化合物を形成し、スパッタリング速度が低下して膜質に影響を及ぼすターゲット被毒を防ぐために、ガス組成を注意深く制御する必要がある。
- 統一性の問題:大型の長方形カソード(1メートル以上)の場合、均一なプラズマ密度、ひいては均一な層厚分布を達成することは難しい。この不均一性は、基板全体の膜特性のばらつきにつながります。
要約すると、スパッタリングは多用途で広く使われている薄膜蒸着技術であるが、限界がないわけではない。これには、膜の汚染に関する問題、低い成膜速度、高いエネルギー消費、膜厚制御の難しさ、材料選択の難しさなどが含まれる。さらに、特殊な装置やメンテナンスが必要なため、このプロセスは高価になる可能性がある。これらの限界を理解することは、スパッタリングプロセスを最適化し、特定の用途に適した成膜方法を選択するために不可欠である。
総括表:
制限 | 主な内容 |
---|---|
フィルム汚染 | 原料からの不純物、ガス状汚染物質、不活性ガス不純物。 |
低堆積率 | 熱蒸発より遅く、蒸着フラックスは不均一。 |
高いエネルギー消費 | 発熱が大きく、冷却システムが必要で、運用コストが増大する。 |
フィルム厚のコントロール | 層ごとの成長が困難、スパッタされた原子の拡散輸送。 |
素材の選択 | 溶融温度による制限、高価なターゲット、非効率的な材料の使用。 |
プロセス・パラメーター | 高い運転圧力、ユーザーによるメンテナンス、複雑な運転ニーズ。 |
反応性スパッタリングの課題 | ガス組成の制御、大型カソードにおける均一性の問題。 |
スパッタプロセスの最適化でお困りですか? 専門家にご相談ください オーダーメイドのソリューションのために!