薄膜ディップ・コーティングのプロセスには、浸漬、滞留、引き抜き、乾燥という4つの主な段階がある。この方法は、基材を溶液に浸漬し、制御された速度で引き抜くことによって、基材上に薄膜コーティングを施すために使用される。このプロセスは、導電性、耐摩耗性、耐食性、光学特性などの表面特性を、用途に応じて変更するために広く使用されている。一般的に薄膜蒸着は、化学的・物理的蒸着法を含む様々な技術を用いて、基材上に薄膜を形成・堆積させることを含む。ディップコーティングプロセスは、制御された厚みと特性を持つ均一な薄膜を得るための、シンプルかつ効果的な方法です。
キーポイントの説明
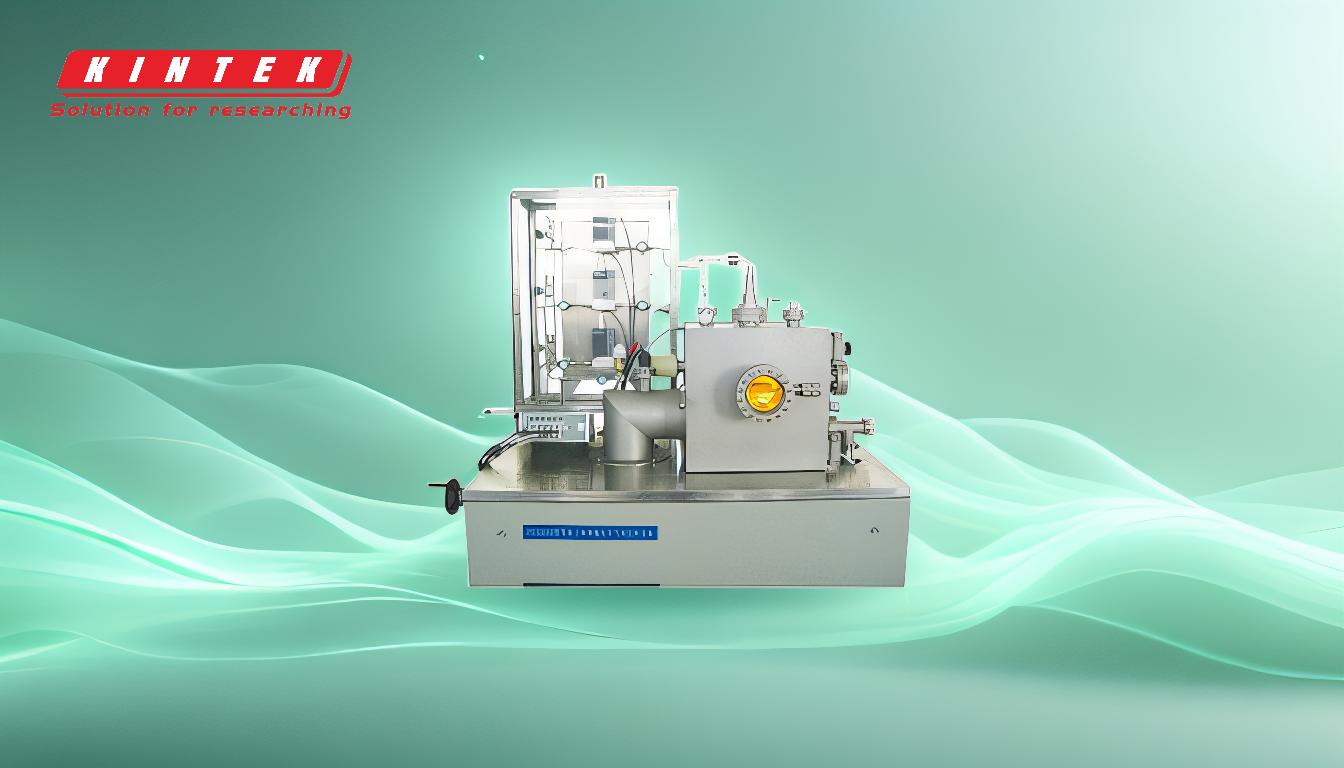
-
薄膜ディップコーティングの段階:
- イマージョン:制御された速度で基板をコーティング溶液に浸す。これにより、基板と溶液が均一に接触します。
- 住居:浸漬後、基材を溶液中に一定時間保持し、コーティング剤が適切に付着するようにする。
- 引き抜き:その後、基材を制御された速度で溶液から引き抜く。引き抜く速度はコーティングの厚さを決定し、速度が遅いほど膜厚は厚くなる。
- 乾燥:コーティングされた基板は、多くの場合、制御された環境条件下で乾燥され、膜を固化させ、密着性を確保する。
-
薄膜蒸着の目的:
- 薄膜蒸着は、導電性、耐摩耗性、耐食性、光学特性の向上など、基板の表面特性を変更するために使用される。
- 電子工学、光学、材料工学などの産業で、部品の性能を向上させるために広く使用されています。
-
薄膜蒸着の種類:
- 化学蒸着:基板表面で化学反応を起こし、固体層を形成する。化学気相成長法(CVD)などがある。
- 物理蒸着:機械的、電気機械的、熱力学的手段を用いて薄膜を成膜する。例えば、スパッタリング、熱蒸着、イオンビーム蒸着などがある。
-
ディップコーティングに影響を与える主な要因:
- 出金スピード:コーティングの厚さを決定します。速度が遅いほど、基材上での溶液の保持力が高まるため、膜厚が厚くなる。
- 溶液粘度:粘度の高い溶液は、塗膜が厚くなる傾向がある。
- 乾燥条件:乾燥中の温度と湿度の管理は、クラックや乾燥ムラなどの欠陥を防ぐために非常に重要です。
-
薄膜ディップコーティングの用途:
- 光学コーティング:ガラスやレンズに反射防止膜や反射膜を形成するために使用される。
- 保護膜:耐食性または耐摩耗性を高めるために金属またはその他の材料に適用される。
- 電子部品:半導体デバイスの導電層や絶縁層の成膜に使用される。
-
ディップコーティングの利点:
- 他の成膜方法と比較した場合の簡便性と費用対効果。
- 複雑な形状や大きな表面を均一にコーティングする能力。
- 引き出し速度と溶液の特性を調整することで、膜厚をコントロールできる。
-
課題と考察:
- 不規則な形状の基板上で均一な厚みを実現することは、難しいことです。
- 欠陥が生じないように、環境条件(温度、湿度など)を正確に制御する必要がある。
- 安定した皮膜を形成できる特定の材料や溶液に限定される。
薄膜ディップコーティングに関与する段階と要因を理解することで、メーカーは、様々な用途に望ましい膜特性を達成するためにプロセスを最適化することができる。この方法は、その簡便性、汎用性、幅広い基材に高品質のコーティングを施す能力において、特に価値が高い。
総括表
アスペクト | 詳細 |
---|---|
ステージ | 浸漬, 浸漬, 放置, 乾燥 |
目的 | 表面特性の改質(導電性、耐摩耗性、光学性など) |
成膜の種類 | 化学的(CVDなど)、物理的(スパッタリング、熱蒸着など) |
キーファクター | 引き出し速度、溶液粘度、乾燥条件 |
用途 | 光学コーティング、保護コーティング、電子部品 |
利点 | コスト効率、均一なコーティング、膜厚のコントロール |
課題 | 不規則な形状の均一性、精密な環境制御が必要 |
薄膜ディップコーティングプロセスの最適化 当社の専門家に今すぐご連絡ください オーダーメイドのソリューションを提供します!