モールド・フィッティングは、金型製造工程における重要なステップであり、金型試運転の前に行われ、製造時の材料シールオフ性能を確保する。この工程は、部品のバリ、ショートショット、余分な材料などの欠陥を防ぐことを目的としている。伝統的に、金型のはめ込みは熟練した職人によって手作業で行われてきましたが、この方法には、非効率、一貫性のなさ、人間の専門知識への依存など、いくつかの限界があります。現代の進歩は、自動化または半自動化ソリューションを導入することでこれらの問題に対処し、精度と再現性を向上させている。
キーポイントの説明
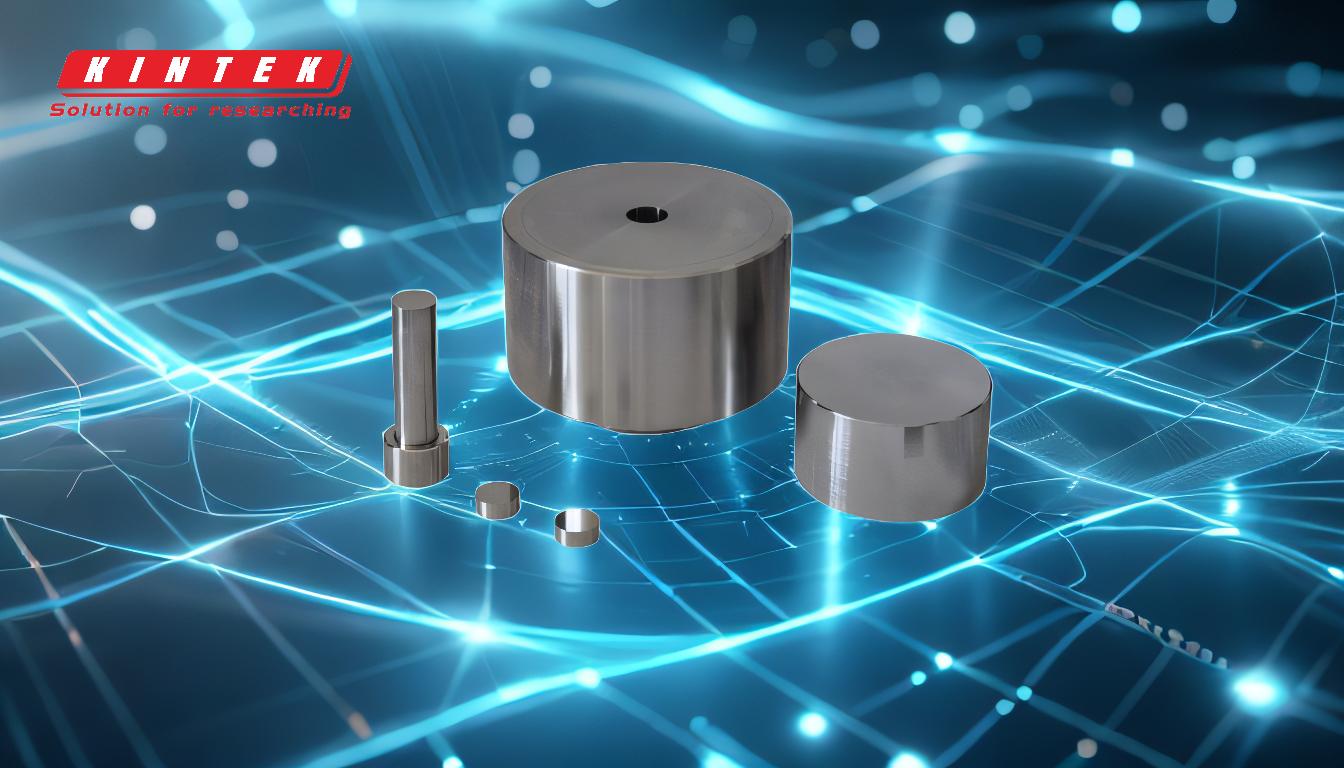
-
金型フィッティングの定義と目的
- 金型フィッティングとは、金型の構成部品が完璧にフィットして、材料射出のための密閉された環境を作り出すプロセスのことです。
- その主な目的は、パーツのフラッシュ(余分な材料が金型から漏れる)、ショートショット(金型への不完全な充填)、余剰材料(不要な材料の蓄積)などの欠陥を防ぐことです。
- このステップは、高品質の生産を達成し、無駄を最小限に抑えるために非常に重要です。
-
金型試運転プロセスにおける重要性
- 金型フィッティングは、金型トライアル(金型の初期試運転)の前に行われ、問題点を特定し修正します。
- 金型のフィッティングが適切に行われることで、生産時に金型が意図した通りに動作し、欠陥やダウンタイムのリスクが低減されます。
- これは、製造工程の効率と費用対効果に直接影響します。
-
伝統的な型はめ方法
- 歴史的に、金型のはめ込みは、熟練した職人が手工具と技術を使って手作業で行っていた。
- この方法は、職人の専門知識と経験に大きく依存するため、時間がかかり、人為的なミスが起こりやすい。
- 手作業は、金型の性能にばらつきをもたらし、最終製品の品質に影響を与える可能性がある。
-
従来の方法の課題
- 非効率: 手作業による金型合わせは労働集約的で、生産スケジュールを遅らせる可能性があります。
- 一貫性のなさ: 人為的ミスにより金型の性能にばらつきが生じ、欠陥につながる可能性がある。
- 技能依存性: 熟練工を必要とするため、経験豊富な職人が不足している地域では制約となる可能性がある。
- コスト: 手作業による金型フィッティングは労働集約的であるため、製造コストが高くなる。
-
金型フィッティングにおける現代の進歩
- 自動化とテクノロジーは、金型取付工程を大きく変貌させています。
- コンピューター支援設計(CAD)やコンピューター支援製造(CAM)システムは、最小限の人的介入で精密な金型フィッティングを可能にする。
- CNC(Computer Numerical Control)マシンなどの高度な機械は、一貫性のある正確な金型フィッティングを実現します。
- これらの進歩は、効率を改善し、コストを削減し、最終製品の全体的な品質を向上させます。
-
最新の金型取付技術の利点
- 精度: 自動化されたシステムにより、金型部品が完璧に組み合わされ、欠陥のリスクを低減します。
- 一貫性: 技術主導のプロセスにより、人為的ミスが排除され、均一な金型性能が得られます。
- 効率: 自動化により金型取付工程がスピードアップし、生産時間が短縮されます。
- 費用対効果: 技術への初期投資は高いかもしれないが、長期的な人件費や材料費の節約は大きい。
-
さまざまな産業での応用
- 自動車、電子機器、消費財、医療機器など、射出成形に依存する業界では、金型フィッティングが不可欠です。
- 各業界には金型性能に対する特定の要件があり、精密な金型フィッティングは品質基準を満たすために不可欠です。
金型フィッティングの重要性と最新技術の利点を理解することで、メーカーは生産工程を最適化し、欠陥を減らし、全体的な製品品質を向上させることができます。
総括表
アスペクト | 詳細 |
---|---|
定義 | 金型部品が密閉された材料射出環境に完全に適合するようにします。 |
目的 | 部品バリ、ショートショット、冗長材料などの欠陥を防止する。 |
従来の方法 | 熟練した職人による手作業。非効率で一貫性がない。 |
最新技術 | CAD、CAM、CNCを使用した自動化ソリューションで、精度と再現性を実現。 |
メリット | 精度、一貫性、効率、費用対効果の向上。 |
用途 | 自動車、電子機器、消費財、医療機器。 |
先進のソリューションで金型取付工程を最適化します。 今すぐ までご連絡ください!