スパッタリングは広く使用されている薄膜堆積技術ですが、効率、コスト、用途の適合性に影響を与える可能性のあるいくつかの欠点があります。これらの制限には、膜の汚染、材料選択の制限、膜厚制御の課題、リフトオフなどの他のプロセスとの組み合わせの難しさなどの問題が含まれます。さらに、スパッタリングでは、成膜速度の低下、冷却要件によるエネルギーコストの高さ、RF スパッタリングでの過熱や DC スパッタリングでの電荷蓄積などの複雑な問題が発生する可能性があります。これらの欠点を理解することは、スパッタリングプロセスを最適化し、特定の用途に適切な堆積方法を選択するために非常に重要です。
重要なポイントの説明:
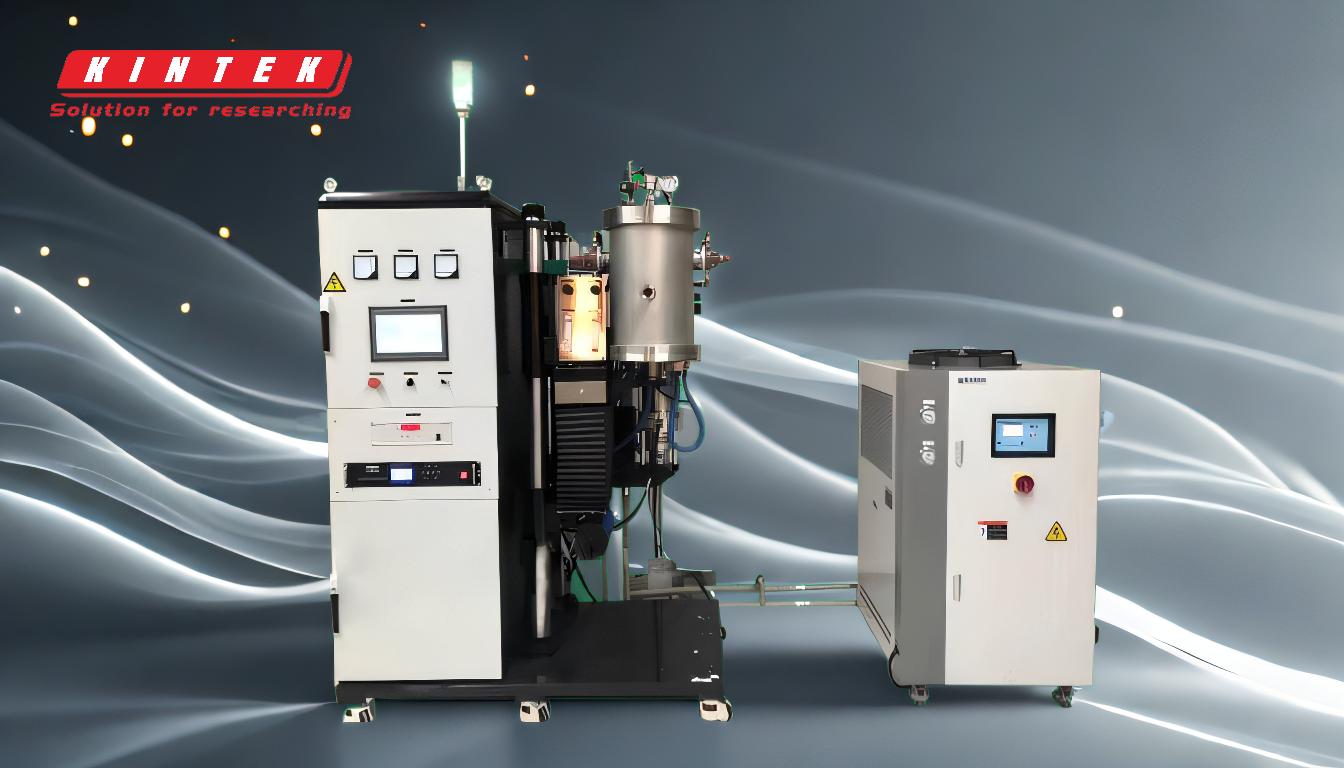
-
フィルムの汚れ:
- スパッタリングでは、ソース材料からの不純物の拡散により膜が汚染される可能性があります。これは、わずかな汚染でもフィルムの性能を低下させる可能性があるため、高純度のフィルムが必要な場合に特に問題となります。
- アルゴンなどの不活性スパッタリングガスも成長膜中で不純物となり、堆積プロセスをさらに複雑にする可能性があります。
-
材料選択の制限:
- スパッタリングプロセスは、ターゲット材料の溶融温度特性によって制限されます。融点が非常に高い材料は、一般的なスパッタリング条件下では原子を効率的に除去できない可能性があるため、スパッタリングが困難な場合があります。
- 絶縁材料は電荷が蓄積し、プロセスが不安定になる可能性があるため、スパッタリングが特に困難です。
-
膜厚制御の課題:
- スパッタリングでは膜厚を正確に制御することができないため、高度に均一な厚さまたは特定の厚さを必要とする用途では重大な欠点となる可能性があります。
- スパッタリング中の原子の拡散輸送により、鋭い界面や制御された層ごとの成長を達成することが困難になりますが、これはパルスレーザー蒸着などの他の蒸着方法を使用するとより簡単に達成できます。
-
低い堆積速度:
- スパッタリングは通常、他の薄膜堆積技術と比較して堆積速度が低くなります。これにより、特に大規模または高スループットのアプリケーションの場合、生産時間とコストが増加する可能性があります。
- スパッタリング中に発生する熱を管理する冷却システムの必要性により、生産率がさらに低下し、エネルギー消費が増加します。
-
高い基板加熱効果:
- スパッタリングプロセスでは基板が大幅に加熱される可能性があり、温度に敏感な材料や基板に悪影響を与える可能性があります。
- 過熱は RF スパッタリングにおける一般的な問題であり、電波を生成するためにより高い電力入力が必要となり、システムへの熱ストレスの増加につながります。
-
リフトオフプロセスとの組み合わせの難しさ:
- スパッタリングは、原子輸送の拡散性質のため、膜構造化のためのリフトオフプロセスと組み合わせることが困難です。これにより、完全なシャドウイングが不可能になり、汚染の問題やパターニング精度の低下につながります。
- シャープなシャドウイングを実現できないと、パターン化されたフィルムの解像度と精度が制限される可能性があり、これは半導体製造などのアプリケーションでは重要です。
-
DCスパッタリングにおける電荷の蓄積:
- DC スパッタリングでは、ターゲット材料に電荷が蓄積するとプロセスが不安定になり、アーク放電が発生する可能性があり、ターゲットや堆積膜に損傷を与える可能性があります。
- この問題は、絶縁材料をスパッタリングする場合に特に顕著であり、電荷の蓄積によりプラズマが中断され、堆積効率が低下する可能性があります。
-
メンテナンスとプロセスパラメータの制限:
- スパッタリング システムでは、きれいな薄膜を実現し維持するために定期的なメンテナンスが必要です。真空システムおよびその他のコンポーネントは、汚染を回避し、一貫した成膜を確保するために最適な状態に維持する必要があります。
- スパッタリングのプロセスパラメータは真空システムの能力によって制限されることが多く、効果的にスパッタリングできる材料や条件の範囲が制限される可能性があります。
結論として、スパッタリングは多用途で広く使用されている薄膜堆積技術ですが、課題がないわけではありません。これらの欠点を理解することは、プロセスを最適化し、特定の用途に適した堆積方法を選択するために不可欠です。汚染、材料の選択、プロセス制御などの問題に対処することで、これらの制限の一部を軽減し、スパッタリングの全体的な効率と有効性を向上させることができます。
概要表:
欠点 | 説明 |
---|---|
フィルムの汚れ | ソース材料またはスパッタリングガスからの不純物は、膜の品質を劣化させる可能性があります。 |
材料選択の制限 | 高融点または絶縁材料は効果的にスパッタリングすることが困難です。 |
厚み制御の課題 | 原子輸送が拡散するため、膜厚を正確に制御することは困難です。 |
低い堆積速度 | スパッタリングは他の蒸着方法と比較して速度が遅くなります。 |
高い基板加熱 | 基板の加熱により、温度に敏感な材料が損傷する可能性があります。 |
リフトオフの難しさ | スパッタリングとリフトオフプロセスを組み合わせるのは困難です。 |
DCスパッタリングにおける電荷の蓄積 | 絶縁材料は電荷を蓄積し、不安定性を引き起こす可能性があります。 |
メンテナンスとパラメータの制限 | 定期的なメンテナンスと真空システムの制限はプロセスの効率に影響します。 |
スパッタリングプロセスの最適化についてサポートが必要ですか? 今すぐ専門家にお問い合わせください カスタマイズされたソリューションを実現します。