蒸留は、広く使用されている分離技術であるが、その効率性、拡張性、特定の文脈における適用性を制限するいくつかの欠点がある。これらの欠点には、揮発性溶媒の損失、カンナビノイドのような熱に敏感な化合物を取り扱う際の課題、高い装置コスト、分離効率と生産時間の制限などがある。さらに、伝統的な蒸留法は、複雑なセットアップやメンテナンスを伴うことが多く、連続運転や大規模運転には実用的ではない。以下では、蒸留の主な欠点について、技術的限界と実用的限界の両方に焦点を当てて詳しく説明する。
主なポイントの説明
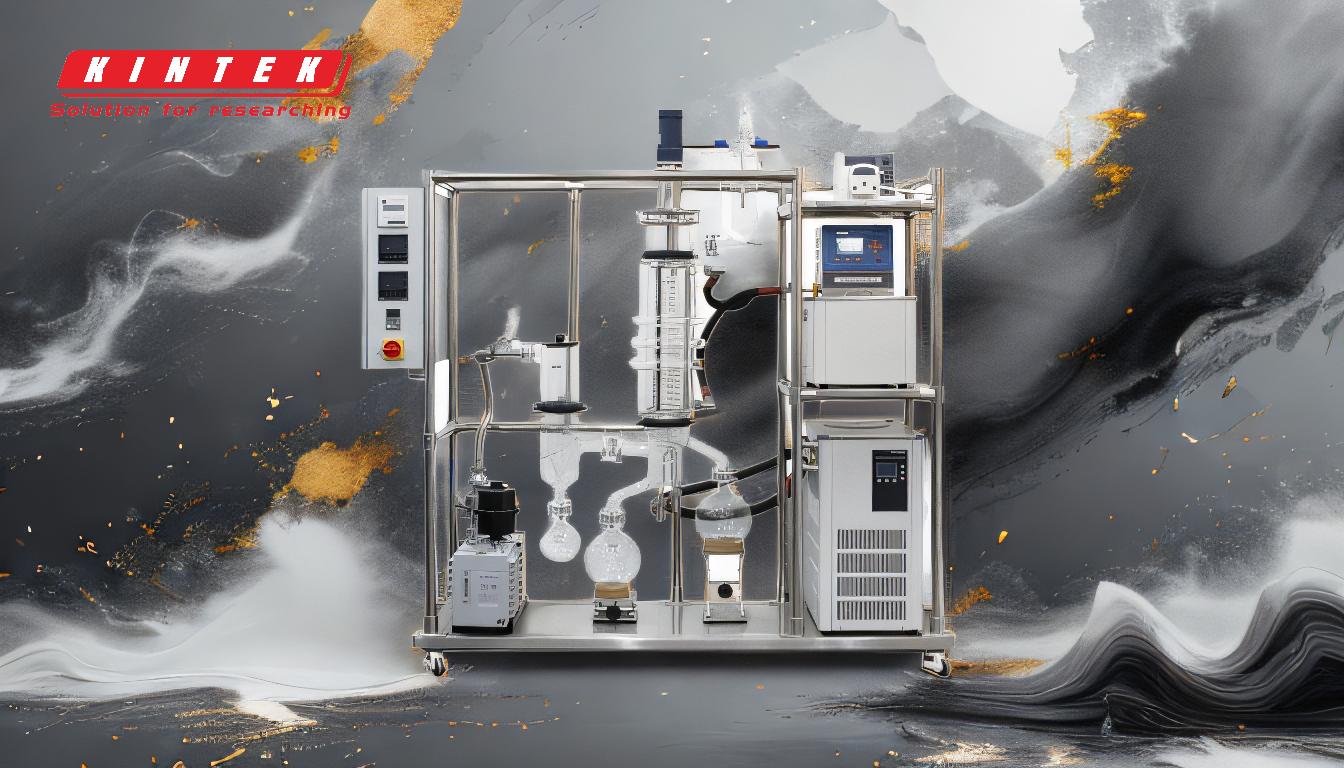
-
揮発性溶剤の損失
- ショートパス蒸留では、蒸発フラスコと受入フラスコ間の距離が短いため、揮発性溶媒が失われることがある。これは、沸点の低い化合物や揮発性の高い化合物を扱う場合に特に問題となる。
- 溶媒の損失は収率を低下させるだけでなく、業界が溶媒回収のより効率的で信頼性の高い方法を求めているため、ショートパス蒸留システムの市場成長も制限される。
-
敏感な化合物の熱劣化
- 蒸留では、沸点に基づいて化合物を分離するために高温を必要とすることが多い。しかし、これはカンナビノイド(CBDなど)のような熱に弱い化合物にとっては有害な場合がある。
- 例えば、CBDは高温で分解されやすく、化学構造が変化して効能が低下する可能性がある。低圧でのショートパス蒸留はこの問題を軽減することができるが、プロセスに複雑さとコストを加えることになる。
-
バッチサイズとスケーラビリティの限界
- 伝統的なショートパス蒸留システムは、小バッチサイズに制限されることが多く、大規模な工業用途には不向きである。
- 産業界では生産需要を満たすために連続処理が必要とされることが多いため、連続供給機能がないことは、その有用性をさらに制限している。
-
低い分離効率と時間消費
- 蒸留の特殊な形態である分子蒸留は、分離効率という課題に直面している。分子蒸留器の設計上、分離率が低くなることが多く、最終製品の純度が損なわれる可能性がある。
- さらに、このプロセスは時間がかかるため、高い処理能力と迅速な生産サイクルを必要とする産業にとっては効率が悪い。
-
高い設備コストと複雑さ
- 分子蒸留システムは、高真空システムと精密な材料密封を必要とするため、設備コストが大幅に上昇する。
- 蒸発・凝縮面の設計とメンテナンスは複雑で、専門的な知識が必要とされ、運用上の課題も増える。
- 高真空度を維持するためには、高度な技術と厳格なメンテナンス・プロトコルが要求されるため、プロセスはさらに複雑になる。
-
面倒なセットアップと洗浄手順
- 溶媒除去のような単純な蒸留方法は、装置のセットアップや洗浄が複雑なため、面倒なことが多い。
- このような手順は労働集約的で時間がかかるため、プロセス全体の効率が低下し、運転コストが増加する可能性がある。
-
小規模システムにおける不整合
- 伝統的なショートパス蒸留で使用されるような小規模蒸留システムは、不整合を起こしやすい。こうした不整合は、温度、圧力、流量のばらつきから生じることがあり、信頼性の低い結果につながる。
- このような制約があるため、一貫した再現性のある結果を必要とする産業にとって、小規模なシステムは魅力的ではない。
要約すると、蒸留は化合物を分離・精製するための貴重な技術であるが、熱劣化や溶媒の損失、高コストやスケーラビリティの問題など、その欠点は特定の用途における代替または補完的な方法の必要性を浮き彫りにしている。産業界は、特定のニーズに合わせて分離技術を選択する際、蒸留の利点とこれらの欠点を慎重に比較検討しなければならない。
総括表
デメリット | 説明 |
---|---|
揮発性溶剤の損失 | ショートパス蒸留は溶媒のロスを招き、収率と効率を低下させる。 |
熱による化合物の分解 | 高温はカンナビノイドのような熱に弱い化合物を分解する可能性がある。 |
バッチサイズとスケーラビリティの問題 | 小バッチに限られ、大規模または連続操作には不向き。 |
低い分離効率 | 分子蒸留は分離率が低く、純度とスピードを損なう。 |
設備コストが高い | 高価な真空システムと複雑なメンテナンスが必要 |
面倒なセットアップとクリーニング | 労働集約的な手順は、運用コストを増加させ、効率を低下させる。 |
小規模システムにおける不整合 | 小規模システムでは、ばらつきのために信頼できない結果が出ることがよくあります。 |
より効率的な分離ソリューションが必要ですか? 当社の専門家にご連絡ください。 にご相談ください!