バイオリアクターの設計には、それがサポートする生物学的プロセスの特定の要件を確実に満たすための体系的アプローチが含まれる。バイオリアクターは、生物学的または生化学的プロセスが実施される制御された環境であり、多くの場合、微生物、細胞、または酵素が関与する。設計プロセスには、適切なタイプのバイオリアクターを選択し、そのサイズと構成を決定し、温度、pH、酸素レベル、攪拌などの重要なパラメーターを監視・制御する機能を組み込むことが含まれる。その目的は、生物または細胞の増殖条件を最適化し、生産性を最大化し、産業応用のためのスケーラビリティを確保することである。
キーポイントの説明
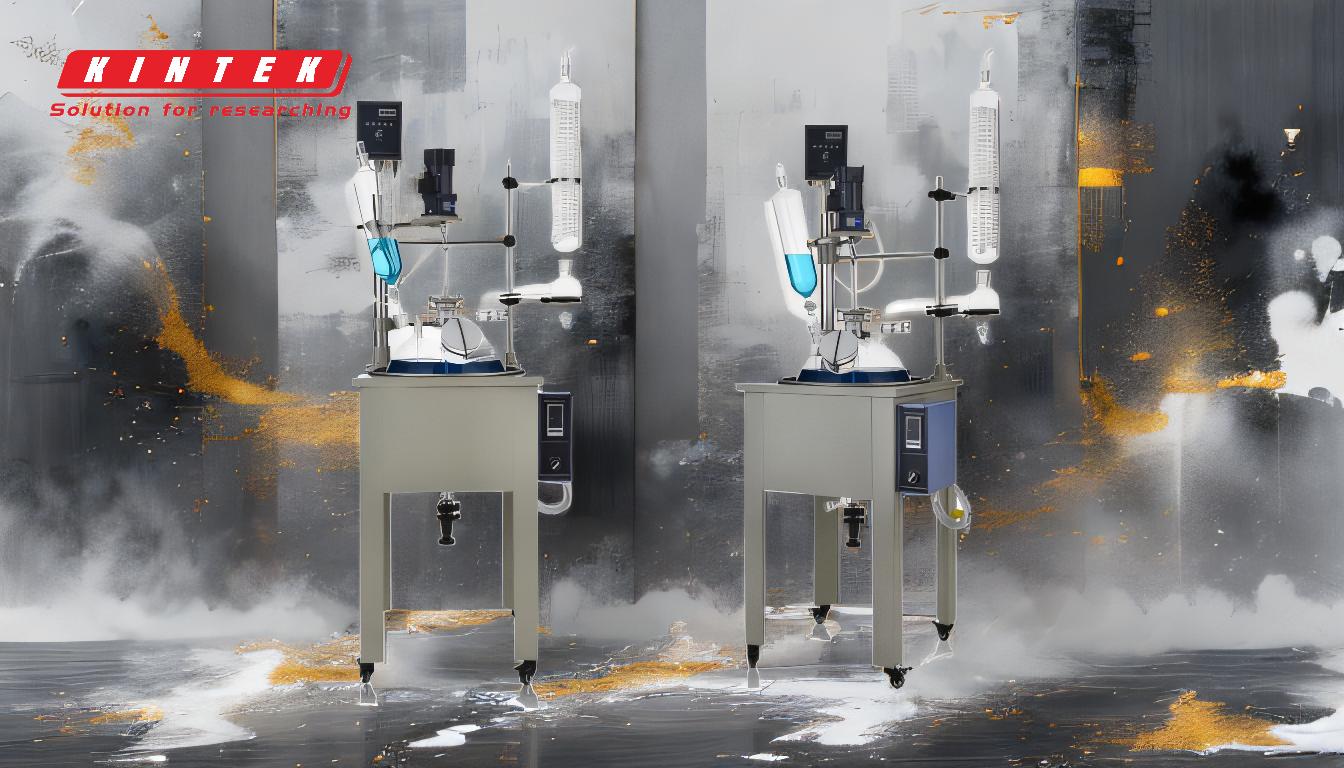
-
目的と要件を定義する:
- 目的:生物学的プロセス(発酵、細胞培養、酵素生産など)と望ましい結果(バイオマス生産、代謝物合成など)を明確に定義する。
- スケール:バイオリアクターが実験室規模の研究用か、パイロット規模の試験用か、本格的な工業生産用かを決定する。
- 生物/細胞タイプ:異なる生物には固有の増殖要件があるため、使用する特定の生物または細胞の種類を特定する。
- 製品:最終製品(タンパク質、バイオ燃料、医薬品など)とその純度要件を指定します。
-
バイオリアクターのタイプの選択:
- 攪拌槽型バイオリアクター:汎用性が高く、良好な混合と酸素移動が可能なため、一般的に使用されている。好気性プロセスに適しています。
- エアリフト・バイオリアクター:空気またはガスを使用して培養液を混合・通気する。せん断に敏感な細胞や低エネルギー投入を必要とするプロセスに最適。
- パックベッド・バイオリアクター:固体支持体上に固定化された細胞または酵素を含む。連続プロセスや細胞密度の高い培養に適しています。
- 膜分離型バイオリアクター:バイオリアクターと膜ろ過システムを組み合わせたもので、廃水処理や細胞と生成物の分離によく使用される。
- フォトバイオリアクター:藻類などの光合成生物用に設計され、光照射が制御されている。
-
サイズと構成の決定:
- ボリューム:必要な生産規模に基づいて作業容積を計算する。ガス交換と発泡抑制のためのヘッドスペースを考慮する。
- アスペクト比:混合効率、酸素移動、放熱に影響する高さと直径の比率を選択する。
- 材質:生体適合性があり、耐腐食性があり、滅菌が容易な材料を選択する(例:ステンレス鋼、ガラス、特殊プラスチック)。
- ポートと接続部:サンプリング、供給、ガス交換、センサー統合用のポートを含む。
-
攪拌・通気システムの設計:
- 攪拌:均一な混合を確保し、細胞の沈降を防ぐために、インペ ラーシステムを設計する。インペラのタイプ(例:ラシュトンタービン、船舶用プロペラ)とその速度を考慮する。
- 曝気:好気的プロセスに十分な酸素供給を確保する。スパージャーまたはディフューザーを設計して、ガスを均等に分配し、 細胞へのせん断応力を最小限にする。
- 酸素移動速度(OTR):生物または細胞の代謝要求を満たすOTRを計算する。望ましいOTRを達成するために、撹拌と曝気システムを最適化する。
-
モニタリングと制御システムの導入:
- センサー:温度、pH、溶存酸素(DO)、圧力などの重要なパラメータをリアルタイムで監視するセンサーを統合。
- 制御システム:自動制御システムを導入し、最適条件を維持する。フィードバックループを使用して、攪拌速度、ガス流量、冷却/加熱などのパラメーターを調整する。
- データロギング:プロセスの最適化と規制遵守のためのデータロギング機能を含む。
-
無菌性と汚染制御の確保:
- 滅菌:オートクレーブ、SIP(Steam-in-Place)、化学滅菌などの滅菌方法に耐えられるようにバイオリアクターを設計する。
- 密封:汚染を防ぐため、高品質のシールとガスケットを使用してください。すべての接続部に漏れがないようにする。
- 空気ろ過:HEPAフィルターやその他の空気ろ過システムを設置し、無菌環境を維持する。
-
拡張性と柔軟性のための最適化:
- モジュール設計:スケールアップやスケールダウンが容易なモジュール設計を検討する。これは、ラボ・スケールから工業スケールの生産に移行する場合に特に重要である。
- 柔軟性:異なるプロセスや生物に対応できるようにバイオリアクターを設計し、研究や生産に柔軟に対応できるようにする。
-
エネルギー効率とコストを考慮する:
- エネルギー消費:特に攪拌・曝気システムにおいて、エネルギー消費を最小限に抑えるよう設計を最適化する。
- 費用対効果:材料や部品のコストと要求性能のバランスをとる。メンテナンスと運用コストを含む総所有コストを考慮する。
-
設計の検証とテスト:
- プロトタイプテスト:設計を検証するためにプロトタイプを作り、テストする。バイオリアクターが望ましい性能基準を満たしていることを確認するための実験を行う。
- プロセスの最適化:プロトタイプを使用して、撹拌速度、曝気速度、栄養供給戦略などのプロセスパラメーターを最適化する。
- 規制遵守:設計が関連する規制基準、特に医薬品や食品製造のアプリケーションに準拠していることを確認する。
-
文書化と反復:
- ドキュメンテーション:計算、材料仕様、試験結果など、設計プロセスの詳細な文書を管理する。
- 反復:テストからのフィードバックを使って設計を改良する。性能、拡張性、および費用対効果を改善するために、必要に応じて反復する。
これらのステップに従うことで、特定の生物学的プロセスに適したバイオリアクターを設計することができ、最適な性能、拡張性、規制遵守を確保することができます。
要約表
ステップ | 主な検討事項 |
---|---|
1.目的と要件の定義 | 目的、規模、生物/細胞タイプ、製品仕様 |
2.バイオリアクタータイプの選択 | 攪拌槽型、エアリフト型、充填床型、メンブレン型、光バイオリアクター型 |
3.サイズと構成の決定 | 体積、アスペクト比、材質、ポート、接続部 |
4.撹拌と曝気の設計 | インペラタイプ、スパージャー、酸素移動速度(OTR) |
5.モニタリングシステムの導入 | 温度、pH、DO、圧力のセンサー;自動制御システム |
6.無菌性の確保 | 滅菌方法、密封、空気ろ過 |
7.スケーラビリティの最適化 | モジュール設計、異なるプロセスへの柔軟性 |
8.エネルギーとコストを考える | エネルギー効率、費用対効果、総所有コスト |
9.検証とテスト | プロトタイプテスト、プロセス最適化、規制遵守 |
10.文書化と反復 | 詳細な文書化、反復的な設計改善 |
お客様のニーズに合わせたバイオリアクターの設計はいかがですか? 当社の専門家に今すぐご連絡ください にお問い合わせください!